Spray concreting is a widely used building method in the UK. Nick Oliver, SOCOTEC’s operations manager, Infrastructure Services, explores the history of the technique and explains why it is vital for this form of concreting to be properly tested before use.
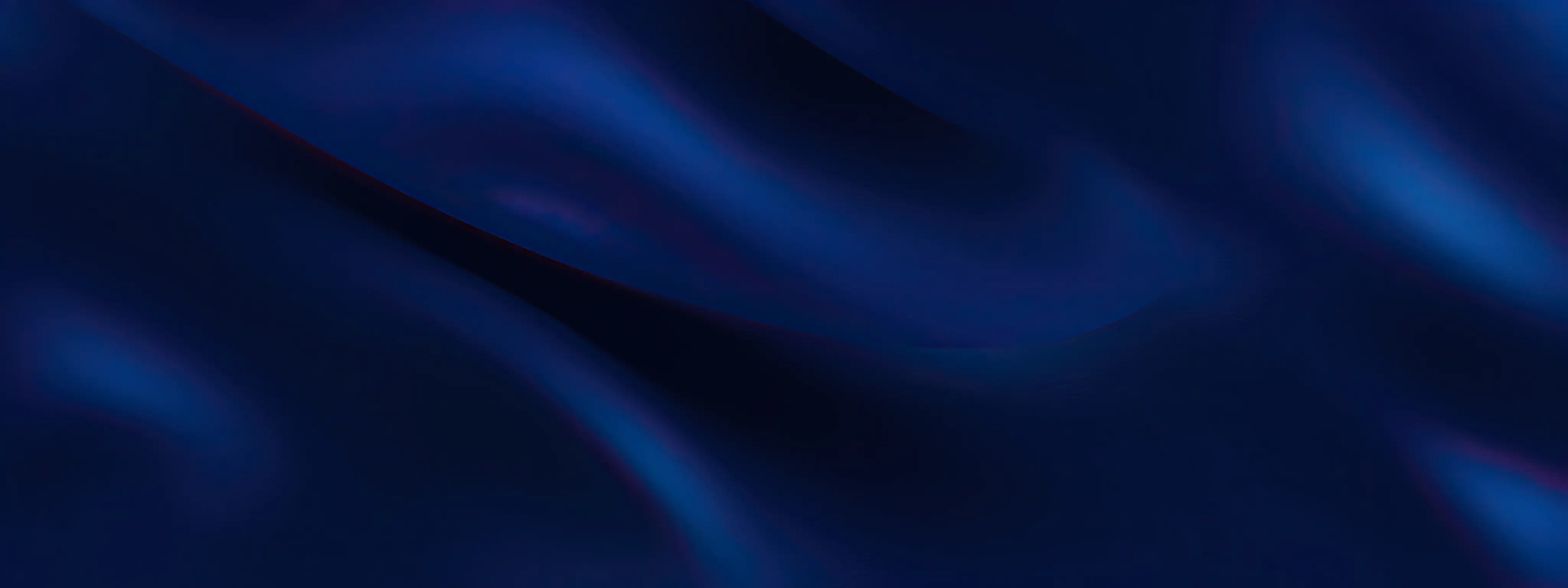
Spray concreting, commonly known within the industry as “shotcreting”, involves the projection of wet or dry mix concrete at a high velocity and letting the material set on the receiving surface. Using this method, the material can be sprayed onto any type or shape of surface, including vertical or overhead areas.
The sprayed concrete has a high, early and rapid strength gain, and is low in permeability, meaning it can provide a solid, waterproof lining, without the need for formwork in an extremely short space of time. For certain applications, such as lining tunnels and subterranean works, this technique is extremely useful.
An unlikely beginning
Although this method is now used every day on large and small projects across Britain, spraying concrete is, relatively speaking, a new building technique. The process actually has an interesting backstory, having first been discovered by a museum curator in Chicago in the late 1890s.
Dr Carlton Akeley, from the Chicago Field Museum, was working on the creation of replica prehistoric animals, attempting to apply mortar over skeletons in an effort to make them more lifelike. Having initially tried and failed to spread the material over the frame using a trowel, he went on to create a crude single chamber pressure vessel which would project a mix of sand and cement over the frames.
Following his initial success, Akeley made several refinements to, what he called, his ‘cement gun’ patenting the technique, and introduced it into global markets. During the Second World War, spraying concrete was actually an instrumental technique in building airport hangers for Spitfires and repairing bombed-out structures in Britain.
In the 1960s, spray concreting technology advanced to include wet mixes. This involved pumping out ready-mixed concrete rather than adding water at the nozzle. The practicality of the technique was quickly recognised by the industry and its use became commonplace for a wide range of applications in the commercial building sector.
Stringent testing
With its increased use, it follows naturally that there was a need for international guidance and legislation to ensure high quality sprayed concrete across Europe.
Anyone working with the material must be up-to-speed with the most recent standard, BSEN 14487, which came into force in 2006. This document outlines requirements for sprayed concrete – these requirements have to be tested, for through a number of quality assurance trials.
When using wet mixes, for example, the batch must be able to meet the requirements of the project, which means testing it in terms of fresh density and workability. Flow tests are a standard method of doing this and involve pouring a sample of the mix onto a table and measuring how far the substance spreads across its surface.
Fibres are often added to sprayed concrete mixes, and in these cases, they must be spread evenly throughout the batch. A fibre washout test, involves counting the number of fibres in a series of small samples, and can prove uniform distribution levels in a batch.
Early age strength tests must also be carried out, involving the use of a penetrometer, an instrument for determining the hardness of a substance, which measures the force needed to insert a needle into set concrete panels. After 24 hours, the concrete is set and a number of cores are extracted and tested for compressive strength, elasticity, shrinkage and permeability to ensure there is no risk of leakage.
As sprayed concrete is required to form a waterproof barrier, permeability tests must ensure that the material cannot be penetrated by liquid. This test sees water being forced onto the surface of the cores for a period of around 72 hours under five bar pressure and then measuring the results.
The compressive strength of concrete changes as it cures which means that any batch needs to be tested periodically to examine its elasticity, proportionality and flexural strength. This involves applying a heavy load onto concrete beams and measuring the results.
After preconstruction trials, any concrete used onsite must then be tested regularly for a site-specific period. If the mix is changed at any time during the project, the new batch needs to also undergo strict testing before use.
Supporting the industry
There is a vast amount of construction activity planned for the UK over the coming years and sprayed concrete is undoubtedly going to be a major part of this. With this in mind, it’s crucial that anyone using this material ensures adequate testing is carried out at every stage of a project. Ultimately, the guidance is in place to help protect workforces and the end-users of new infrastructure, and also to prevent costly delays by keeping timelines on track.
With a fully equipped concrete testing team covering the length and breadth of the UK, able to operate 365 days a year, SOCOTEC can provide a flexible and comprehensive service to prove the quality of sprayed concrete, wherever and whenever necessary.
Want to find out more about SOCOTEC's accredited concrete testing services?
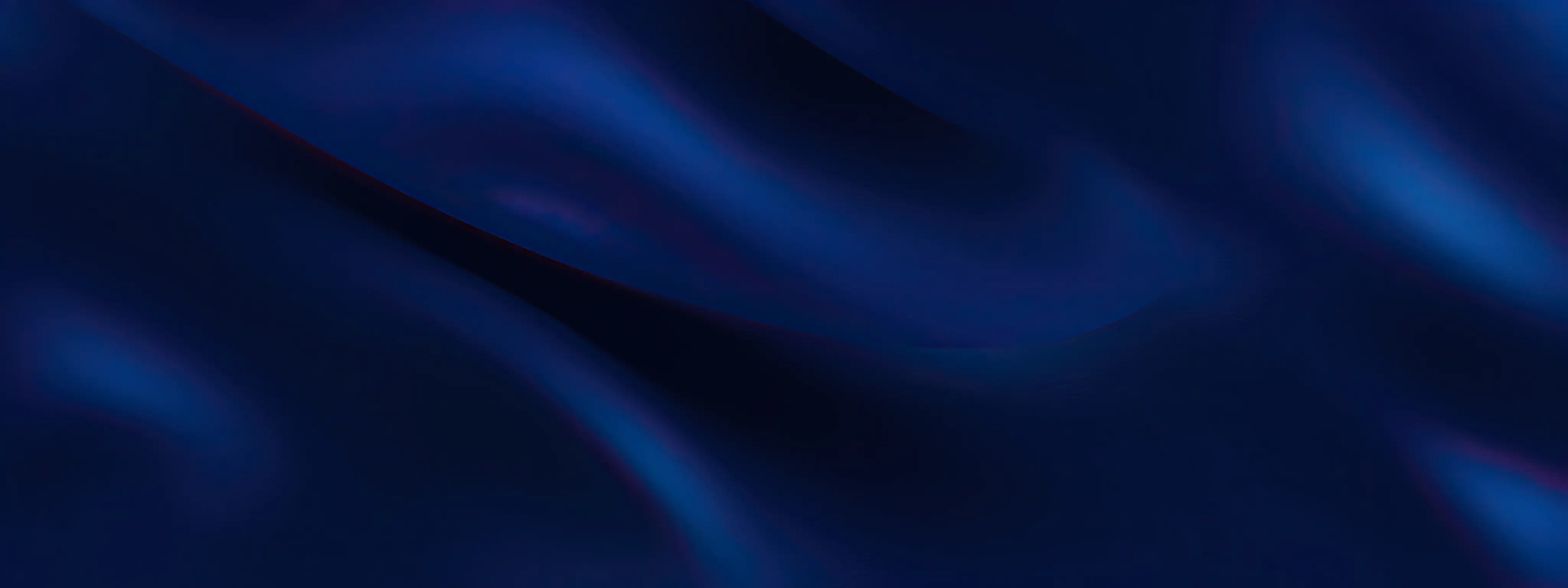
You might also like
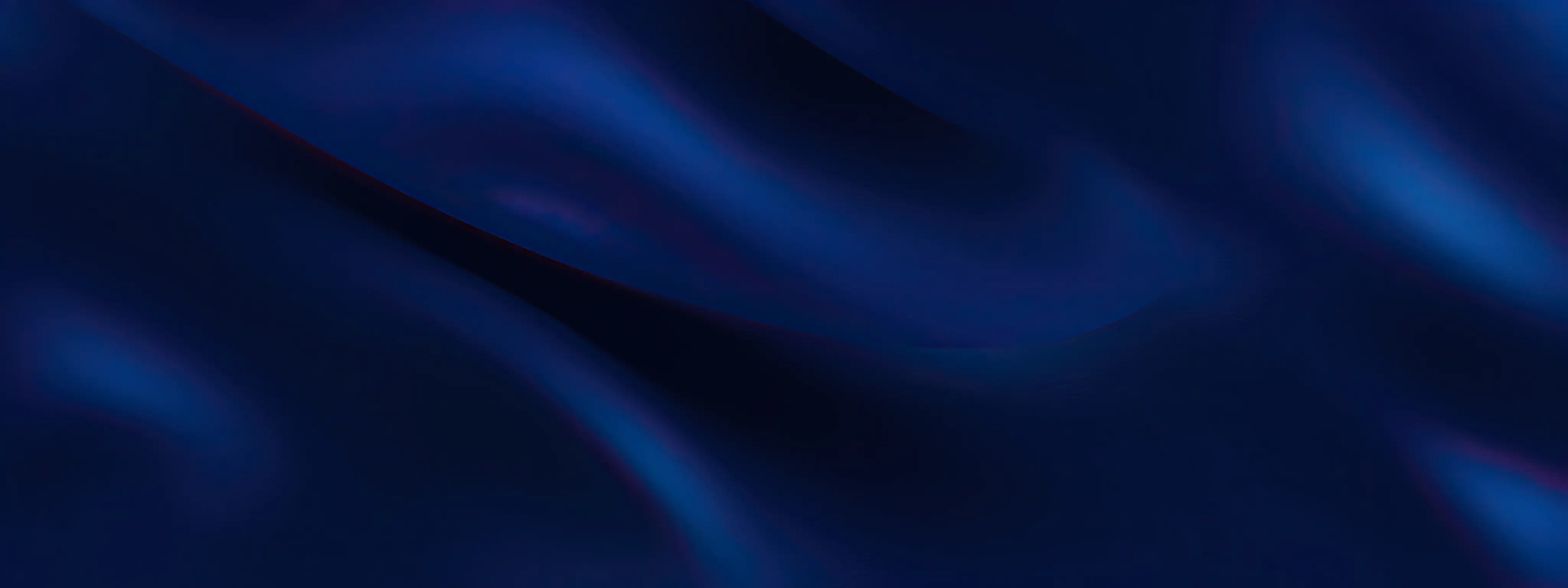
Add new comment