As project manager for Air & Emissions division of SOCOTEC, Andy Tiffen often gets asked ‘what is QAL3?’ and 'what is the real purpose behind QAL3 checks?' Here, he breaks through some of the technical jargon to demystify the QAL3 test in the European Standard BS EN 14181 - Stationary Source Emissions: Quality Assurance of automated measuring systems.
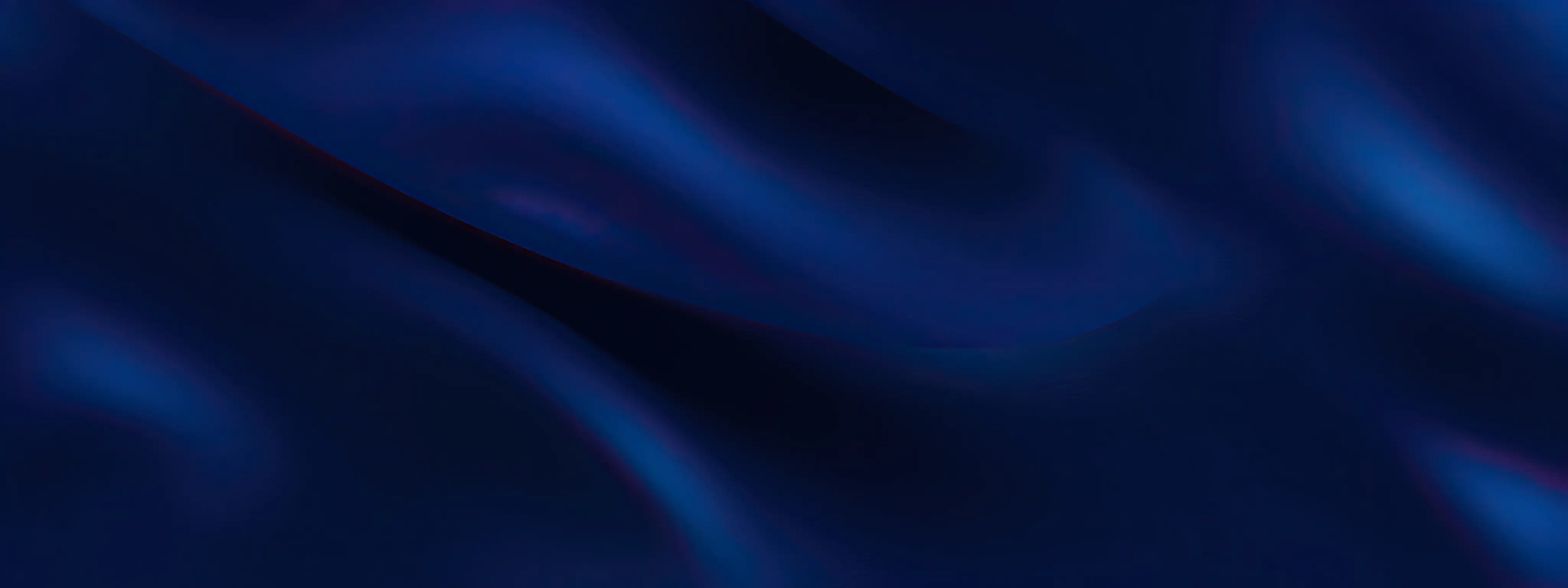
Here, he breaks through some of the technical jargon to demystify the QAL3 test in the European Standard BS EN 14181 - Stationary Source Emissions: Quality Assurance of automated measuring systems.
So what is QAL3?
The actual definition of a QAL3 is a process or procedure which maintains the quality of the Continuous Emission Monitoring (CEM) System.
The actual definition of a QAL3, according to the BS EN 14181:2004, is “a procedure to maintain and demonstrate the required quality of the measurement results during the normal operation of an AMS, by checking that the zero and span characteristics are consistent with those determined during QAL1”.
But actually, the principle behind the QAL3 checks is the same principle that instrument engineers have been following for many years. One question you should be asking is…
…if you were in charge of the calibration of a critical pressure sensor on site, how would you handle it?
Personally, I would get a pressure gauge checker and test the sensor with a known pressure to see if it reads correctly. Let’s say we pump it up to 500mbar… if it reads 500.00, I would be happy and leave it well alone. If it reads 499.98, I’d be satisfied that it was close enough and still leave it well alone. However, if the reading was 426.3, I’d want to adjust it and bring it back to true. That done, I would need to decide when to revisit the pressure gauge and repeat the tests again. As it was a reasonably quick job, I would perhaps consider a week.
The following week, if it reads 500.06, I’d have some confidence in it and let it carry on. Perhaps one more week goes by and now it’s at 500.13; then a week later 500.25 and next it’s 500.41. Any competent instrument engineer would recognise that the figure was slowing creeping up, and perhaps adjust the pressure gauge.
If the figure got higher every time I checked it, I would send it off for repair. On the other hand, if the figure doesn’t change after checking it at weekly intervals, I would reduce the number of checks and just do it once a month.
Control Charts
In very basic terms, the above process is a QAL3 check but quality assurance and consistency across the industry called for a formalised process.
Instead of an engineer using personal judgement to determine if a reading is ‘close enough’, QAL3 uses control charts with alarm levels to determine if a reading is consistently good enough or if a reading is constantly shifting in a single direction.
To decide if a reading is acceptable or not, a “SAMS” value is used as an alarm level. The SAMS value can be set using a number of techniques; it might be based on user experiences, set by the supplier or based on a percentage of the site Emissions Limit Value (ELV). The type of control chart used and how the SAMS is chosen is not fixed within BS EN 14181 and the site operator can select whichever technique is most appropriate.
CEM system adjustments
An Annual Surveillance Test (AST) evaluates the CEM to ensure it functions correctly and the calibration function that was derived during a QAL2 is still valid.
Adjusted CEM systems are a common cause of failures for Annual Surveillance Tests (ASTs) under BS EN 14181. Adjustments are permitted under certain circumstances but how and when they are done must be understood to avoid false fails of the CEM system at the next QAL3 or AST.
Firstly, if a system does automated zero adjustments on a regular basis, then this is normal and is permitted (assuming that the auto zero system was part of the system when it was certified). Also, just like our instrument engineer example above, adjustments can be made if a significant shift in the reading is seen. The QAL3 control chart will determine if the shift in response is significant. The problem is ensuring that any adjustment you make does not upset the QAL3 result. If you make an adjustment to the CEM, the control chart needs to know that adjustment has been made or it will be seen as a step change and cause a QAL3 fail. Only certain types of control chart can accommodate an adjustment such as the CUSUM chart.
In addition to the effect on a QAL3, any adjustment must be assessed for the effect it will have on an existing QAL2 calibration function. For example, consider 4 QAL3 zero check results of -6.1, -6.2, -5.8 & -6.3. These results won’t cause a failure of a QAL3 check as the difference is small and random but it may be tempting to adjust the reading up to get the result to 0.0. However, you may have a calibration function in use of Y = 1X + 6. This function is adjusting the -6 result up to zero and any adjustment of the CEM would increase the chances of a fail at the next AST.
Advice
If I could give one piece of advice, from many years of experience, it would be to: use a type of control chart and alarm level that makes sense for your application, only make adjustments when necessary and ensure any adjustment that is made does not affect the QAL3 or the existing calibration function.
For more information or advice, please get in touch with the Air & Emissions team on 0845 603 2112
Want to find out more about SOCOTEC's services?
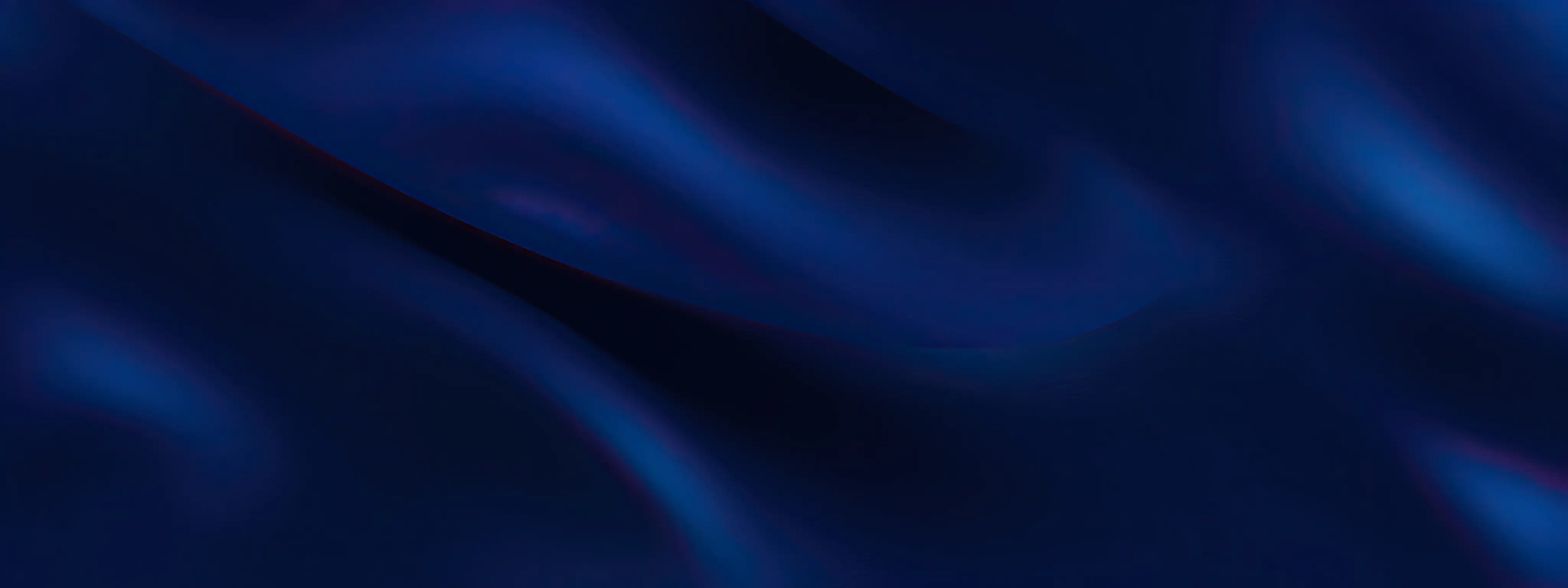
You might also like
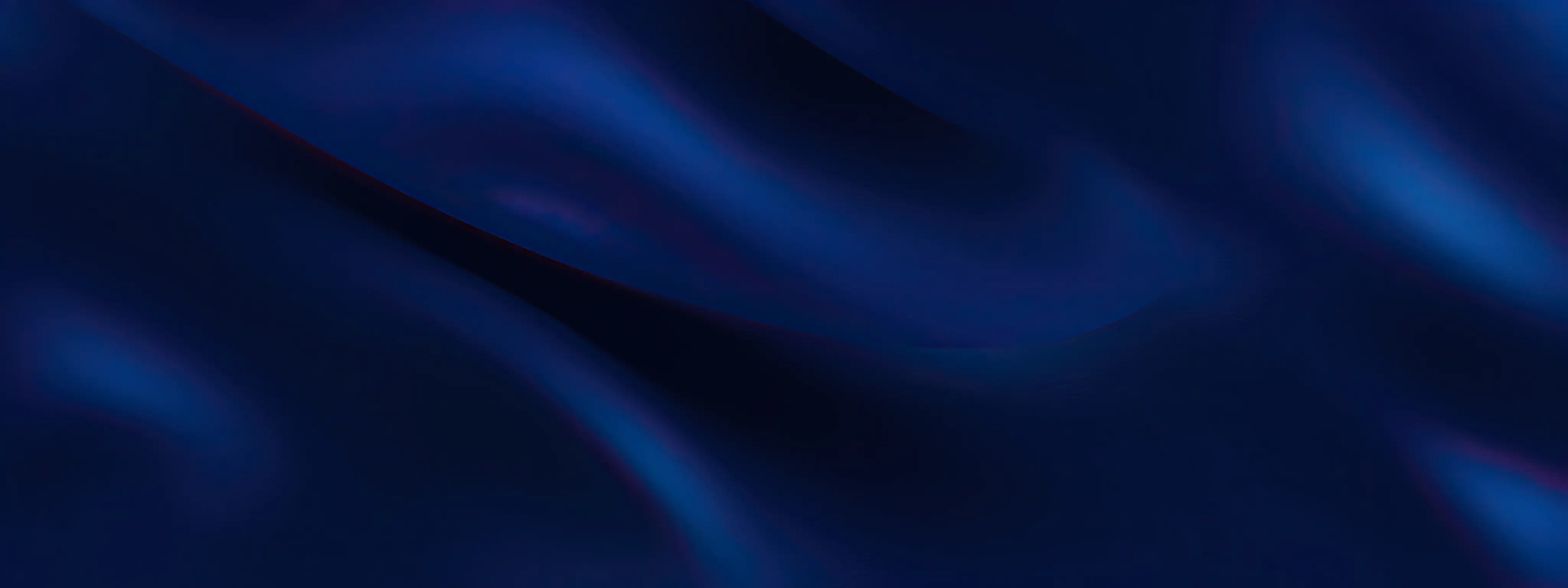
Add new comment