Despite the challenges posed by COVID-19, the UK rail industry is currently going through one of the largest rolling stock replacement programmes of recent times, with the introduction of new rolling stock leading to the withdrawal of various types of rail vehicles. Some of these vehicles are being overhauled or re-purposed for future use, while many are destined for the breakers yard.
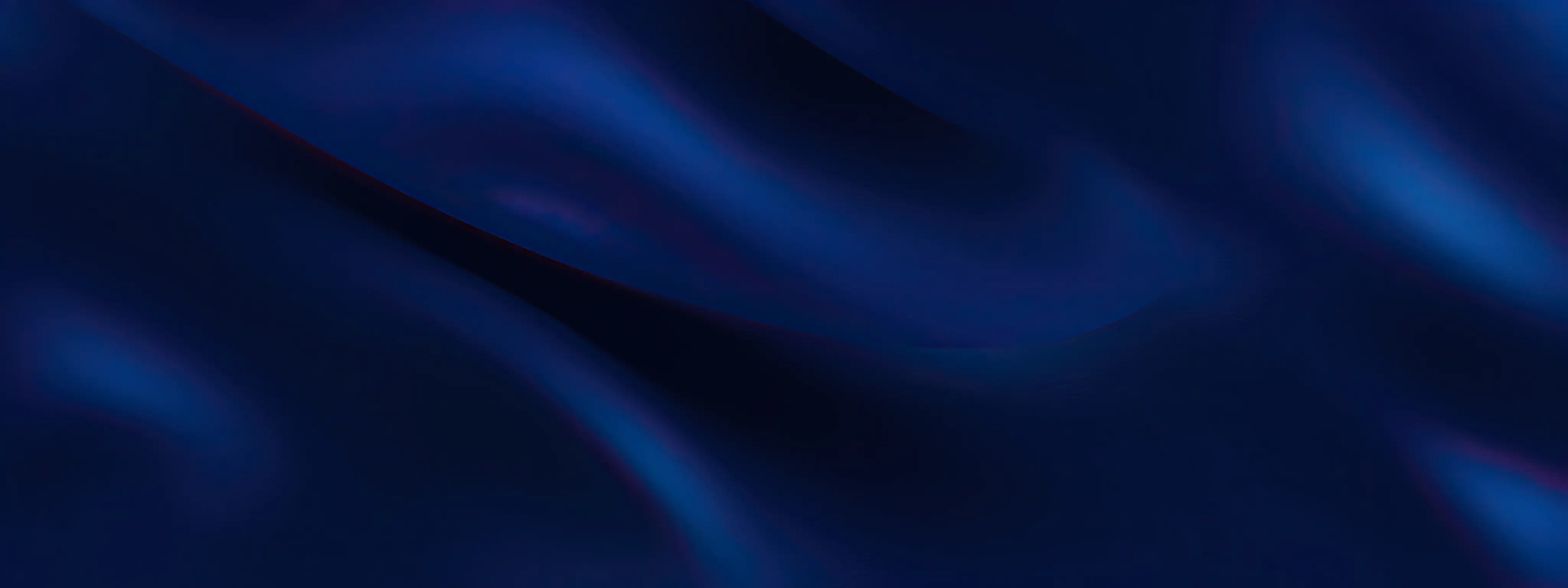
Given the age of some of the withdrawn stock (with some over 40 years old), there is an increased possibility of environmentally or occupationally hazardous materials being present within their fabric or structure. While the issue of asbestos within rolling stock has been recognised for many years, there are a host of other materials that, due to their nature and composition, may also be considered hazardous.
What are hazardous materials and where can they be found within rolling stock?
Hazardous materials are classified as materials and substances which, due to their presence in a particular vehicle or area, pose a potential threat to the health and safety of staff, members of the public or the environment. Their presence may be due to their inclusion in the original construction and subsequent use of the vehicle, or their introduction at a later date via use, renovation or refurbishment. Alternatively, in the case of moulds and fungi, their presence may be due to the degradation of the vehicle as a result of disrepair or storage.
SOCOTEC has substantial experience in surveying railway rolling stock to test for the presence of hazardous materials prior to refurbishment or scrapping. Materials covered within hazardous materials surveys include (but are not limited to):
Lead and lead oxides
Lead and lead oxides were used for many years in various paints and coatings, and while its current use is strictly controlled, many older rail vehicles feature paints which contain copious levels of lead. Until the mid-1960s, white lead (lead carbonate/lead sulphate) was added in substantial quantities as the main white pigment in some paint products, having been intended for use as a primer or topcoat over metal and wood. Lead-based pigments – such as lead tetroxide and calcium plumbate (red lead) – were widely used as an anti-corrosive primer, coating exterior steelwork up until the early 1970s, while red, yellow, orange or green lead-based pigments (lead chromate) were added to decorative coloured gloss paints.
Cadmium and chromium salts
Cadmium and chromium are all naturally occurring metals which, together with many of their compounds, exhibit a wide range of hazardous and toxic properties. Historically, cadmium and chromium salts were used as additives in paints and coatings. Chromium salts such as lead chromate were used to produce bright yellow colours, while zinc chromate was widely used in primers for painting metal.
Various cadmium salts are used in paint pigments – namely, cadmium sulphide (yellow pigment) cadmium selenide (red pigment) and cadmium sulphoselenide (orange pigment). They are mainly used within polymers and plastics due to their vibrant colours and durability, featuring within brightly coloured plastic furniture and wall panelling.
Oils and hydrocarbon residues
A wide range of hydrocarbon-based products (including diesel fuel oil, engine lubricant oil, gearbox oils, hydrostatic oils, antifreezes and greases) are used in the rail industry, and unidentifiable liquids or residues may be present in vehicles. Other on-board components such as transformers, high voltage switch gear and compressors may also contain oils. Many of these are suspected carcinogens and come under the Control of Substances Hazardous to Health (Amendment) Regulations 2004 (COSHH), as well as being flammable and potentially harmful to aquatic life. In addition, the actual structure of the vehicle may be contaminated with hydrocarbons due to leaks from on-board storage tanks or supply pipework.
Chemicals, dust and debris
Numerous chemicals such as lubricants, sealants and cleaning products are used in the rail industry, and residues may well be present on vehicles. Many of these may be toxic, corrosive or otherwise harmful to health and sit under COSHH 2004. Water remaining in engine cooler systems, radiators and compressed air reservoirs may also contain treatment chemicals, additives or possess chemical properties that could pose hazardous when released.
A wide range of products which give rise to dusts are also used within the rail industry. Air handling and other ventilation-related components such as ductwork provides the ideal environment for dust and debris to settle out of air flows and accumulate over time. Many of these dusts contain residues of whatever contaminants were present within the air.
Polychlorinated biphenyls (PCBs)
PCBs are commonly used to describe a range of manmade chemicals called polychlorinated biphenyls, belonging to a class of organic compounds known as chlorinated hydrocarbons. These were often added to insulating oils due to their fire resistant/retardant properties and inherent chemical stability. The most extensive use of PCBs occurred within dielectric fluids (used in electrical capacitors) and insulating oils (used in electrical transformers and HV power equipment). Over time, many capacitors develop leaks due to metal seams in the casing breaking open. In these instances, oil that contains PCBs can contaminate the outer casings or their surroundings.
Many small low voltage units were permanently sealed but sometimes developed leaks due to failed seals and seams. Meanwhile, larger high voltage units (25Kv AC) were designed to be in service for longer periods of time and were subject to regular insulating oil changes. Over time, insulating oil degrades due to oxidation and off gassing, resulting in reduced insulating capability and, in severe cases, unit failure due to explosion. Subsequently, the insulating oil is regularly changed, being drained out via valves fitted near the bottom of the units.
During oil changes, leaks often occurred via draining, refilling, failure of welds and corrosion, resulting in the contamination of the structure around the transformers. While the manufacture and use of PCBs has been outlawed for some time, older rolling stock may still contain PCB residues due to previous usage.
Biohazards
Biological hazards (biohazards) refer to biological substances that pose a threat to the health of living organisms. Examples commonly encountered include bodily fluids, human tissue, blood, human/animal waste and waste products from medical use. While obvious materials such as blood, sputum and faecal waste can contain diseases and viruses, other non-obvious materials could also potentially contain biohazards.
Stagnant water within on-board toilet system components – including water storage tanks, pipework and hot water heaters – or residues left in CET waste tanks may contain high levels of bacteria (such as coliforms, Legionella and E.coli), some of which may pose a risk to health should the water become atomised or form a fine spray during removal. Other potentially harmful contaminants (such as CET tank treatment chemicals) may also be present within the water. Other materials commonly found in vehicles (such as moulds, yeasts and fungi) also pose a risk to health, especially if spores become airborne.
Manmade Mineral Fibre (MMMF) present in insulation materials
Manmade mineral fibre is renowned for causing irritation to the upper respiratory tract/skin and is controlled under COSHH 2004. It is commonly found as rolled insulation material in vehicle roof spaces, as well as slab insulation within cavities between body side walls. Its other common use is as pipe insulation, either as metal clad moulded sections or as loose fill material.
Blown insulation foams
Polymer foams (typical used as wall/floor cavity insulation and in passenger seating) are formed using chemicals called blowing agents. For many years, Chlorofluorocarbons (CFCs) were used as blowing agents due to their low toxicity, low chemical reactivity and low flammability. However, during the 1980s, it was discovered that CFCs were responsible for depletion of the Earth’s Ozone layer due to their persistence within the atmosphere and their reactions with UV light in the upper stratosphere.
Following the withdrawal of CFCs under the 1987 Montreal Treaty, many foams were manufactured using Hydro-chlorofluorocarbons (HCFCs) as blowing agents. While these do not harm the Ozone layer as much as the compounds they replace, they do contribute to global warming. Many polymer foams also contain compounds that provide a degree of fire protection. A widely used compound was Hexabromocyclododecane (HBCDD) – a persistent, toxic and Ecotoxic chemical with bio-accumulative and long-range transport properties.
Due to their environmental persistence and the threat posed to the Ozone layer, the disposal of materials contaminated with/containing CFCs, HCFCs and HBCDD is tightly controlled.
Refrigerant gases
HVAC units fitted on-board rail vehicles contain refrigerant gases that act as a heat transfer/cooling medium. Various gases may be used, the most common being R-134A and R-404A. Nearly all of these gases are based on Hydrofluorocarbons (HFCs), and while they possess low Ozone depletion properties, their atmospheric concentrations and contribution to greenhouse gas emissions are rapidly increasing. As such, HFCs should be captured by degassing and retained for correct disposal.
Other materials and components of note
Other materials and components present in vehicles may also pose a hazard due to their construction or composition. All Gas Discharge Lamps (GDLs) are included within the scope of the Waste Electrical and Electronic Equipment (WEEE) Directive and are identified under the Hazardous Waste regulations. This includes fluorescent lighting tubes, which are widely used on passenger vehicles. Smoke detectors frequently contain a small quantity of radioactive Americium (Am-241) or Radium (Ra-226), and are subject to special regulations (Environmental Permitting Regulations), in addition to the WEEE regulations.
Would your rail organisation benefit from SOCOTEC’s hazardous material survey service?
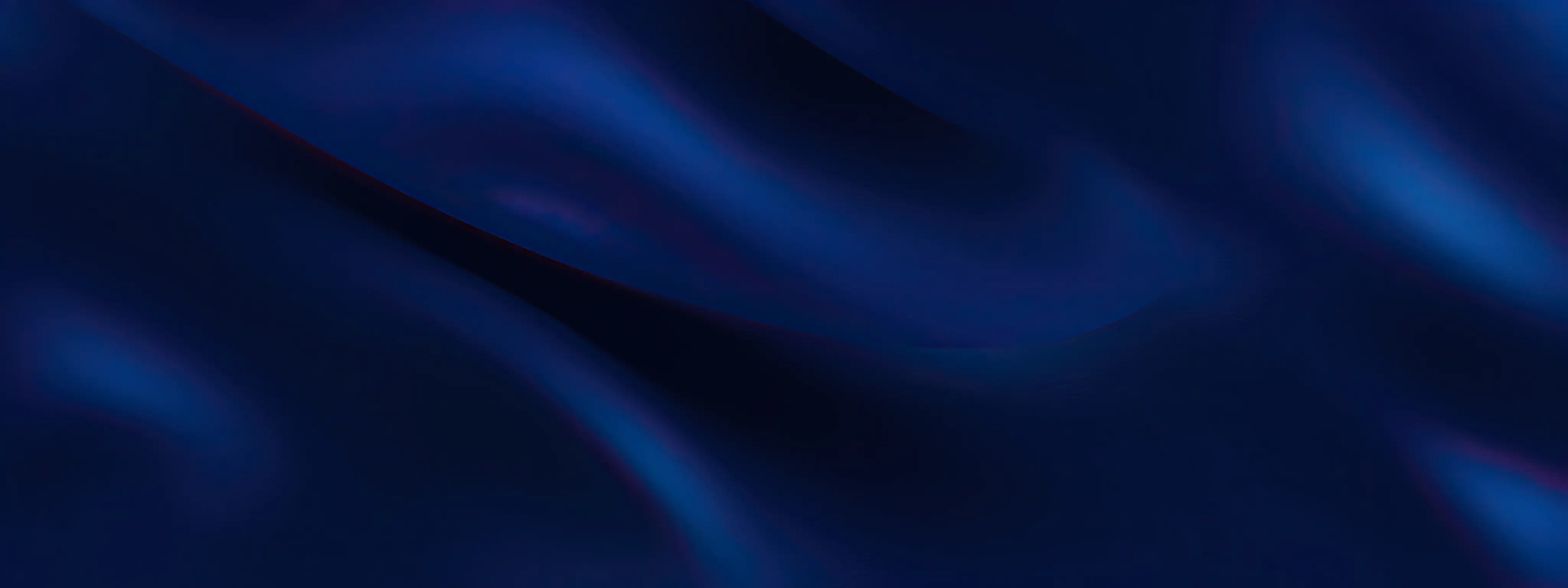
You might also like
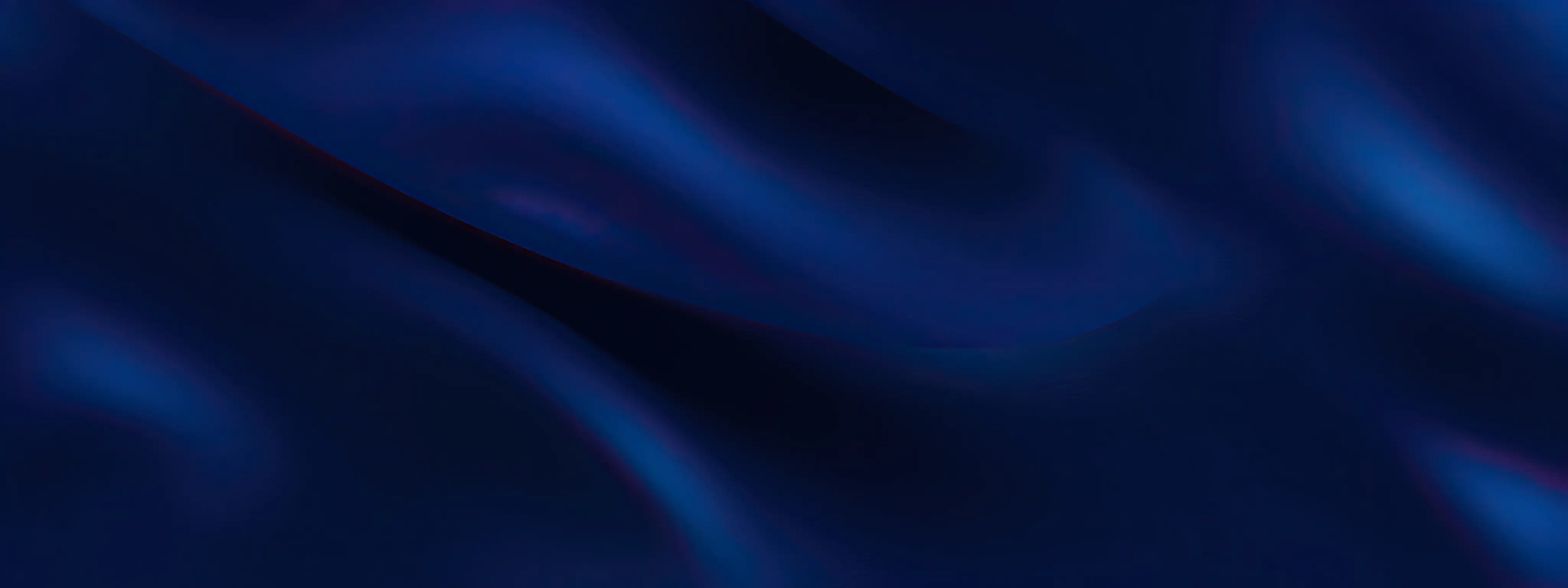
Add new comment