SOCOTEC has a long history of providing oil testing to the rail sector, with its dedicated laboratory dating back to before the privatisation of British Rail in 1996. We work with clients across the rail industry, including operators like Virgin Trains, manufacturers such as Siemens, as well as Network Rail.
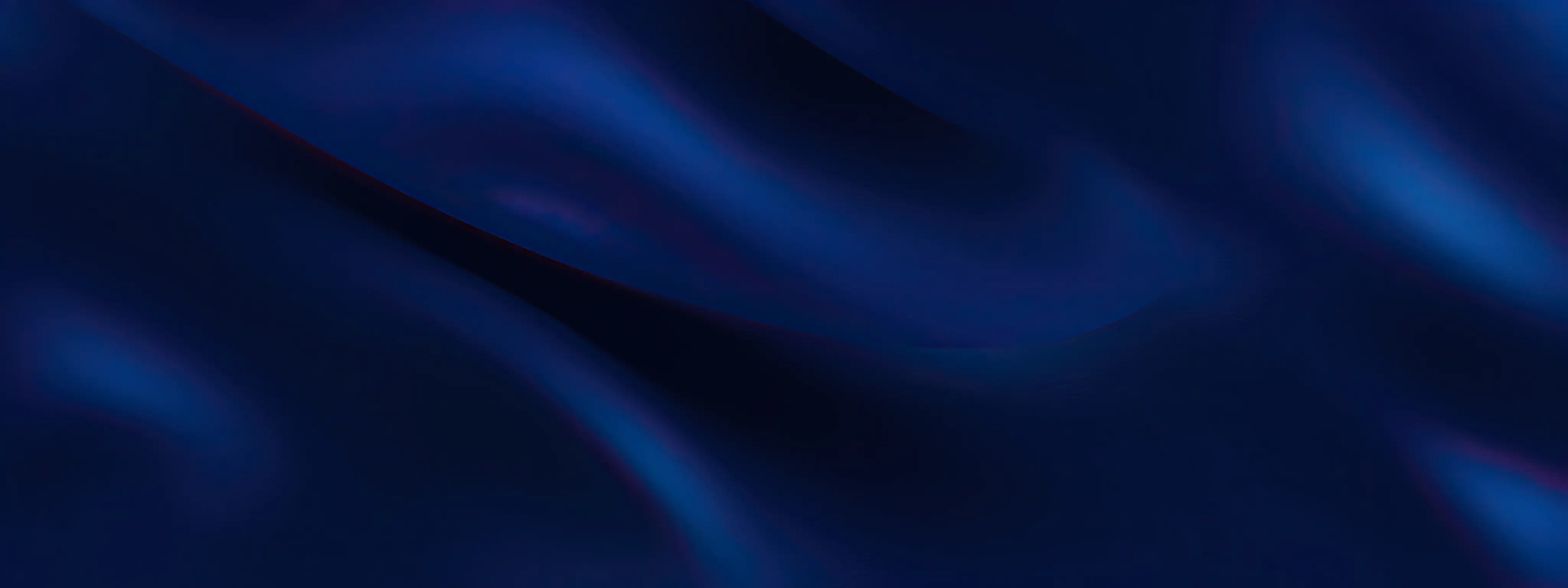
Oil and lubricant testing has become increasingly important across the rail industry in recent years, due to the breadth of information it provides around the long-term performance of assets, in terms of both operational reliability and safety. However, SOCOTEC is often asked questions about the purpose of oil analysis and even the processes involved to take and study the samples.
With this in mind, I’ve answered a few of the most common queries we receive at SOCOTEC:
Why test oil?
Oil analysis is sometimes compared to blood testing. Just as a blood sample alerts doctors to a patient’s health issues, oil tests allow mechanical problems to be identified early, enabling organisations to carry out targeted maintenance to rectify wear and tear well in advance of a component failure, saving time and money in the long-term.
Lubricants, can provide a crucial indication of the integrity of the components they are used on. The detection of metal particles in the fluid can allow SOCOTEC to alert organisations to issues with premature wear which, if left to continue, could lead to a component failure and potential safety issues.
Testing can also give information about the quality of the oil used to maintain rail machinery. Analysis of viscosity, additive content and acidity can all help determine whether the oil is suitable for use on particular components, and how long it will last before needing to be replaced, while testing for contaminants can help identify substances, such as water, coolant, fuel or dust, which could have a negative impact on component integrity.
Which components can be tested?
SOCOTEC tests oil from a wide range of components located throughout the train, including everything from a train's engine, gearbox and transmission, to the compressor, coolant and fuel systems, as well as its transformer if it is electric-powered. Even the lubricants in the axle bearings and traction motors are analysed.
Each of these integral parts of the train require a specific type of lubricant to ensure it offers optimum performace throughout its lifetime. As a result, SOCOTEC tailors tests to the fluid and application in question to provide an accurate picture for clients.
How are tests conducted?
SOCOTEC provides sampling kits for clients to use, and arranges for them to be sent back to the laboratory. The method used and amount of oil removed depends on the component, so kits are tailored to ensure samples are taken correctly.
Once the samples arrive at SOCOTEC’s laboratory, a wide range of techniques are employed to study the oil, including spectrometry, automated titration, and gas chromatography. These methods are vital to determine the physical and chemical characteristics of the fluid, as well as identify potential contamination issues. The data gathered is managed by SOCOTEC’s Laboratory Information Management System (LIMS) to allow the organisation’s expert team to interpret the results accurately.
How long does it take?
The turnaround times for testing can vary; we adhere to our client's requirements. For safety critical parts, such as the gearbox, tests are typically carried out within 24 hours.
SOCOTEC feeds results to clients using a cloud-based reporting system, which significantly speeds up the reporting process to allow clients to take action straight away. It also enables end users to incorporate any guidance, where necessary, straight into their maintenance schedules, further streamlining their management processes. In the event of a safety critical fault being identified, SOCOTEC also provides direct communication to the control centre of a train operating company, alerting them so they can remove the train in question from service as soon as practicable.
How often should tests be carried out?
The frequency with which oil analysis needs to be undertaken varies, and depends ultimately on why clients might want to test their components in the first place. Safety critical components are, understandably, sampled more frequently than others – typically weekly or monthly.
In general, non-safety critical components, and those that are less vital to the reliability of the train, are sampled quarterly or annually.
What are the benefits of testing?
Having a good understanding of component integrity is not just important for ensuring mechanical reliability, it is crucial for ensuring the safety of passengers and rail workers.
Oil testing can help clients understand how their components and lubricants are working day to day. This can give them the tools they need to extend the lifecycles of these materials, keeping their rolling stock and other equipment in optimum working condition.
Comprehensive service
By offering a complete service, from sampling kit to reporting, SOCOTEC plays a major role in enabling clients to enjoy the maximum benefit from oil testing. In doing so, the organisation gives the rail sector the tools it needs to continue to uphold the highest standards of safety for workers and passengers, while also enabling them to minimise the cost of maintaining modern railway technology.
Want to find out more about SOCOTEC's rail services?
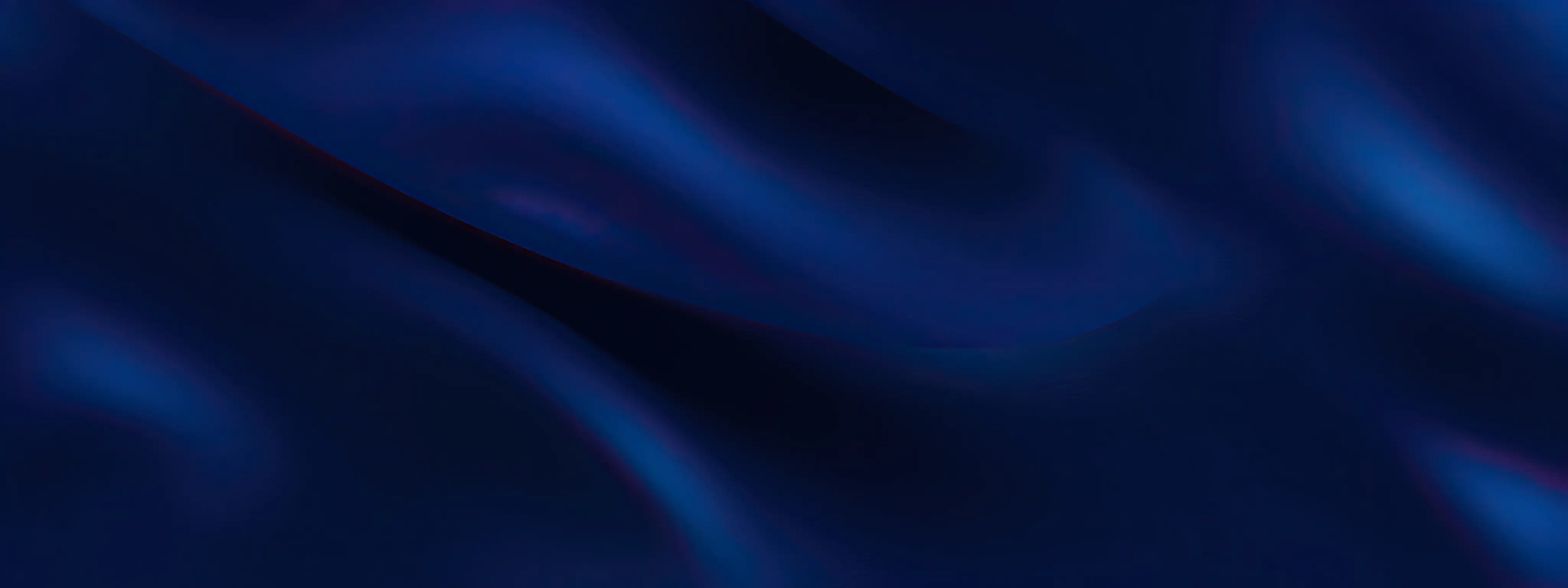
You might also like
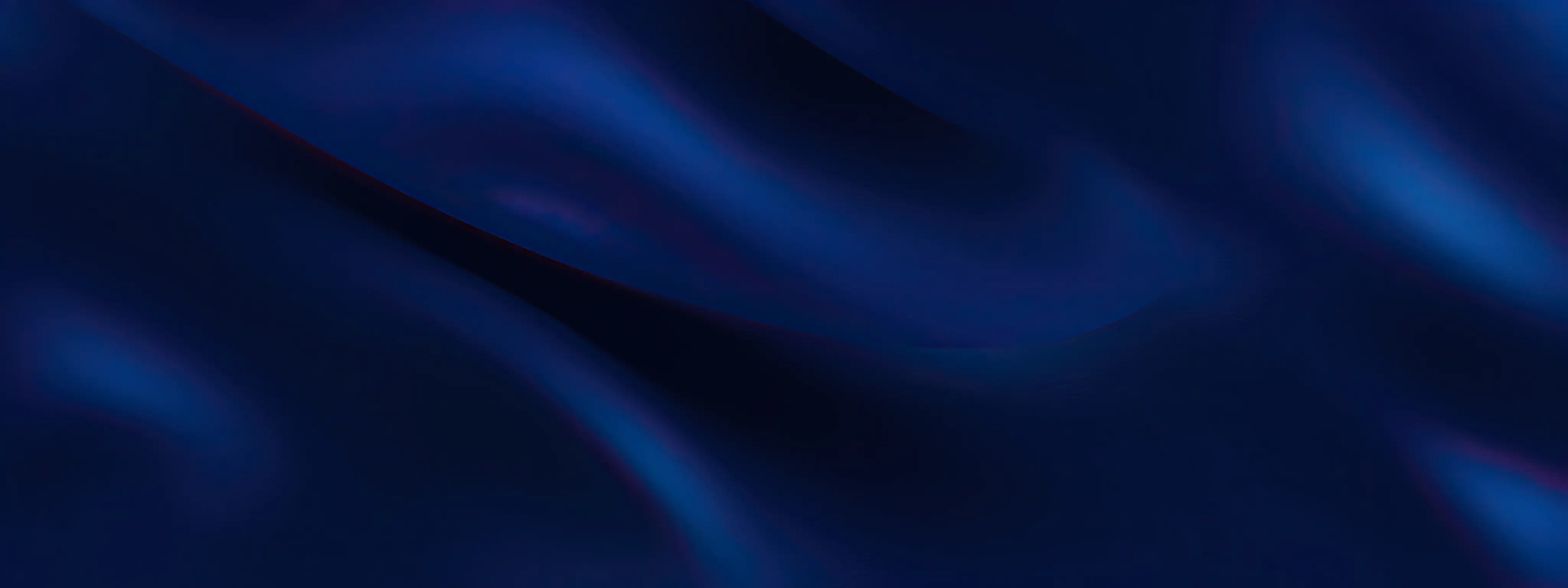
Add new comment