Syngas – an abbreviation for synthesis gas – is a flammable mixture comprising hydrogen, carbon monoxide and various hydrocarbons.
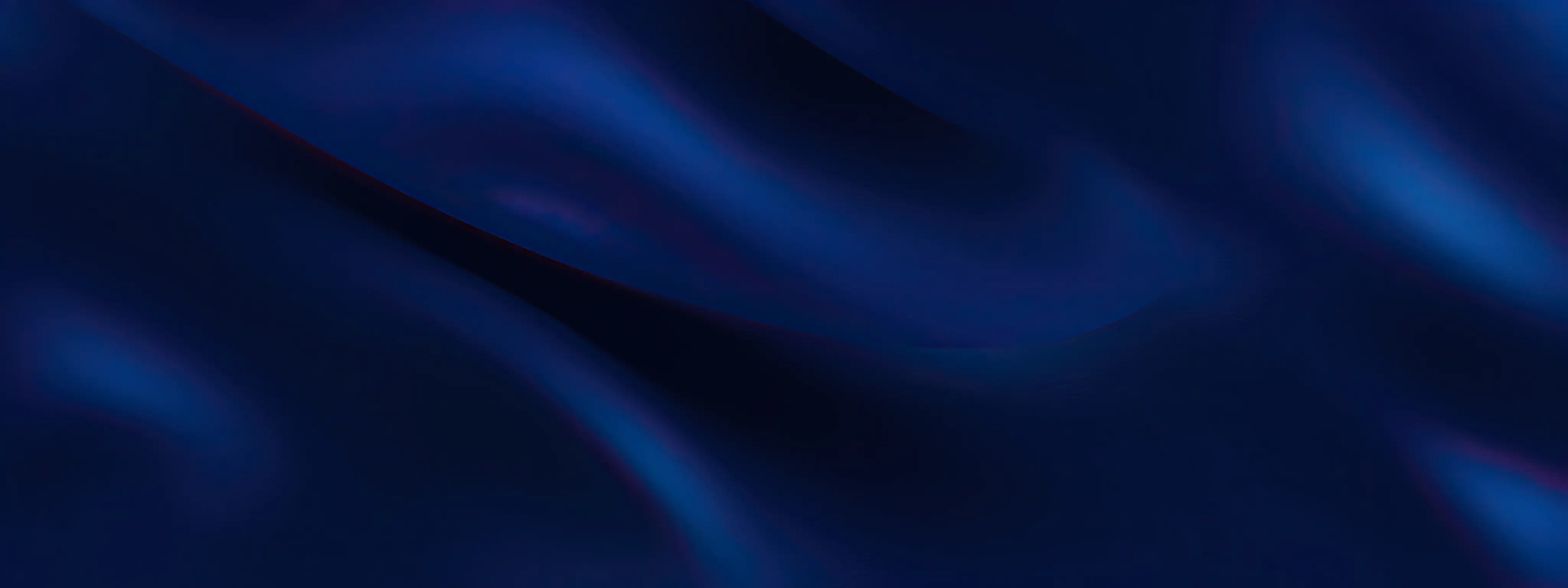
Its name derives from its ability to synthesise other chemicals and act as an intermediary, generating a synthetic natural gas that creates ammonia and/or methanol.
Here, Daniel Bignell, one of SOCOTEC’s senior analysts who is directly responsible for the creation of the organisation’s syngas method, explains how syngas is produced and analysed, as well as detailing how SOCOTEC can provide a range of services to assist your business with any syngas-related requirements.
How is syngas produced?
Syngas is produced via a process known as pyrolysis. In simple terms, this is where a feedstock of organic materials – which range from wood pellets to household waste – are fed into a container, which is sealed and brought to a vacuum before being heated to temperatures exceeding 500 degrees Celsius in a controlled oxygen environment. This thermochemical process converts these organic materials into synthetic gas, which is released from the feedstock and can be combusted to generate electricity.
How do biogas and syngas differ?
Biogas is produced via anaerobic digestion, whereby the feedstock is placed into an oxygen-free container (exactly the same as in the case of syngas production). However, instead of heating biogas, bacteria are used to break down any organic materials.
What are the major challenges of syngas production and analysis?
The main challenge of syngas analysis is ensuring sample integrity at the point of sampling, as the gas is produced under vacuum and can easily be contaminated with air. It is therefore essential that leak testing sample lines are undertaken prior to the testing taking place. Failing that, the samples should be taken from a line with positive pressure. Another issue to consider is that sample lines can be tricky to maintain, as it has been found at a number of waste to energy plants that they can get clogged with a tar-like substance.
With regards to syngas analysis, we have found the biggest challenge to be the improper use of sample media, as well as delays in sending samples into the labs. While reusing sample media such as Tedlar or FlexFoil bags – which are the preferred sampling methods for syngas – is thought to be economical, it has in fact caused several issues. For one, sample integrity can be affected, as the bags are designed for single-use only – re-use can weaken the valves and allow the sample to leak. Overfilling samples is another issue that we have experienced with sample media; this causes the seams on the bags to weaken and potentially tear or burst, creating a health and safety issue and causing the sample to be lost.
Another huge challenge we face is sample effusion. While these bags are specifically designed as gas-containing media, they are not completely infallible as time passes. Hydrogen in particular tends to effuse through the lining of the sample media, which can cause a reduction in quality and may produce a non-representative sample. The solution to this is to get your samples into the lab as quickly as possible, either by courier or by contacting SOCOTEC directly and asking for a collection.
How does syngas relate to biomass?
Syngas and biomass relate in that they are both organic waste feedstocks that undergo anaerobic (oxygen deficient) processes to release gas for the production of energy. They are both renewable and release less particulates into the atmosphere by avoiding direct burning.
Why did SOCOTEC develop a syngas method?
Over the years, the gas laboratory at SOCOTEC has evolved alongside its customer base and their ever-changing requirements. The lab was originally known as the mine air lab, which involved the analysis of samples across the mining sector; however, as our client base changed and developed, SOCOTEC expanded its methods to meet a range of environmental and energy-related demands.
The syngas method was developed as a direct response to the change and increase in client demand. One of our clients’ samples has significantly raised levels of CO and H2; the labs were originally set up for low levels of these gases, but the higher levels proved challenging to analyse. To ensure thorough analysis, samples would have to be diluted, and this would lead to a reduction in both the efficiency and reliability of the results. Therefore, in order to measure the compounds directly without leading to dilution, the CO/H2 (or syngas) method was developed.
Since its original inception in 2017 – which comprised an exhaustive validation process involving sample stability tests and proving method accuracy based on known standards – SOCOTEC has gained UKAS accreditation on its syngas method. This was achieved in late 2018, making the organisation one of the first UK laboratories to offer this service to a nationally recognised standard.
What analysis services do SOCOTEC offer in relation to syngas?
SOCOTEC currently works with an ever-expanding client base of waste to energy plants throughout the UK, assisting them with a wide variety of analytical needs that include but are not limited to gas analysis, Dangerous Substances and Explosive Atmospheres (DSEAR), ventilation monitoring, metals and fuel analysis. There is also significant demand for dust monitoring, including dust explosivity analysis, fugitive dust, nuisance dust and dust-related analysis for a host of occupational health-related issues.
A wide range of syngas testing methods are also available depending on customer requirements, with core analyses involving the measurement of hydrocarbon content, hydrogen and carbon monoxide. These compounds are the main components we look for and are used to generate a Calorific Value (CV) from the latest British Standards.
Additional key compounds offered as part of SOCOTEC’s core syngas suite are oxygen and carbon dioxide. As aforementioned, the environments involved in the production of syngas and biogas are oxygen-deficient, so measuring oxygen provides a good quality control check of these samples. Meanwhile, carbon dioxide is a product of combustion which acts as an important indicator for the quality of the ‘front end’ processes. Excessive moisture within the feedstock can cause fracturing of water; this releases oxygen, which then allows for combustion to take place within the chamber.
What direction is research around syngas currently taking?
The syngas field is constantly evolving, with new issues and solutions occurring on a near daily basis. There are also a number of different conditions within the various types of gasifiers and modifications that companies are making.
Want to find out how SOCOTEC can support with syngas production and analysis?
Get in touch with our friendly team today.
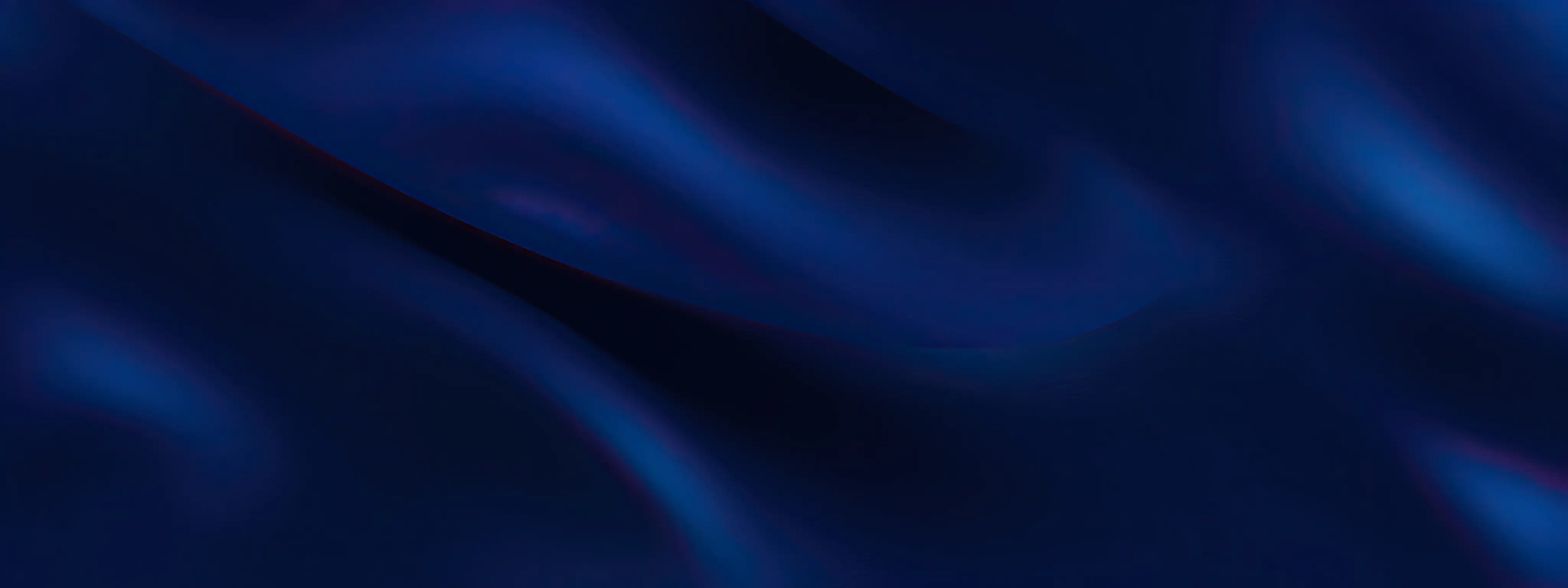
You might also like
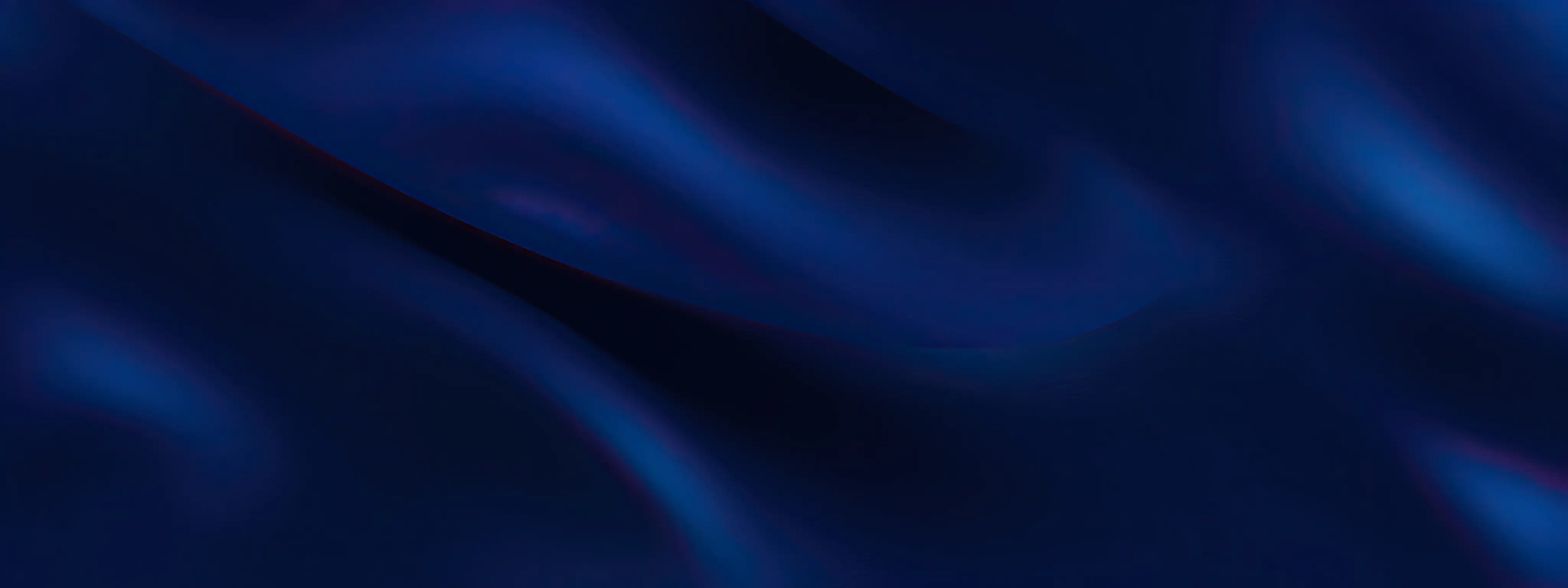
Add new comment