In February 2019, the Health and Safety Executive (HSE) published a bulletin entitled Change in Enforcement Expectations for Mild Steel Welding Fume, and released detailed guidance for employers in November of the same year.
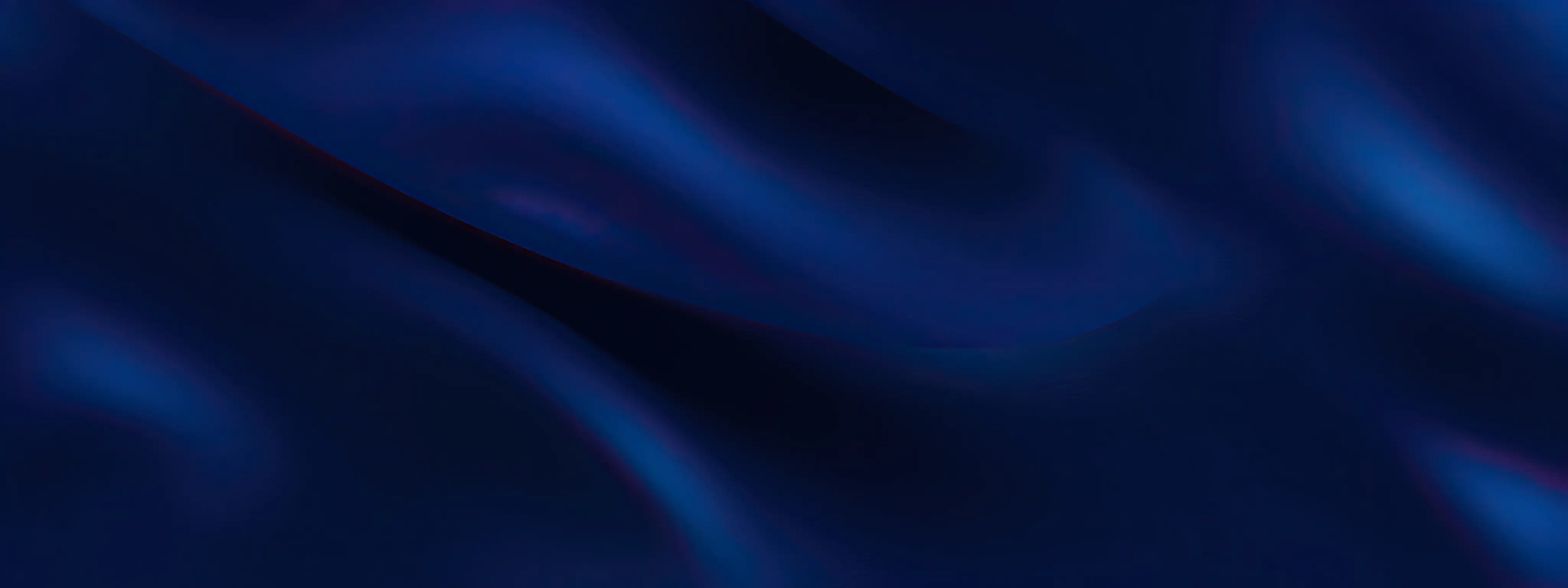
This new change is likely to affect all businesses where any type of welding is undertaken, particularly if local exhaust ventilation (LEV) is not being used.
It is well established that exposure to high concentrations of welding fume can have life-threatening or career-ending health effects, such as pneumonia, occupational asthma and Parkinson’s-related symptoms. What’s more, chromium and nickel from stainless steel welding have long been known to be carcinogenic. However, in July 2018, the International Agency for Research on Cancer (IARC) classified all welding fume and UV radiation from welding as Group 1 carcinogens, indicating that there is sufficient evidence to say that they cause cancer in humans.
This reclassification led to the HSE’s change in enforcement expectations, with controls required regardless of the duration of welding. These include:
- Suitable engineering controls, eg LEV, must be used for all welding activities indoors
- If these controls are unable to control fume capture, respiratory protective equipment (RPE) is required in addition to the engineering controls
- RPE must be worn for outdoor welding if LEV is not reasonably practicable
What do these new changes to welding enforcement mean?
HSE’s updated guidance explains in detail what these changes mean in practice, as well as providing advice on how to comply. The table below, taken from the HSE’s WL3 guidance, summarises what is considered good control practice for welding fume:
At first glance, it might appear that the guidance is not as strict about LEV as the initial change in enforcement expectations. The first line, for example, shows that for sporadic, low intensity MIG welding, good general ventilation and RPE would be acceptable if the LEV is not reasonably practicable.
However, sporadic is defined within WL3 as ‘occasional welding carried out less than once per week, which is incidental to a business’ core activity and cannot be planned for, such as repair or maintenance work’. Low intensity is defined as welding that lasts for less than an hour of the welder’s shift. Care needs to be taken that the work undertaken truly fits within these definitions.
Caution is also needed with regards to the phrase ‘reasonably practicable’. The example given in WL3 is working at height, where the difficulties in moving an LEV system into place could make it not reasonably practicable. However, for many other mobile welding tasks, moving a portable LEV system would still be reasonably practicable, albeit slightly awkward.
The HSE guidance also makes it clear that the first thing an employer should consider, even before LEV, is how to reduce the amount of fume generated on site. This goes back to the hierarchy of control, where eliminating the hazard is always at the top. Can cold joining techniques be used? Would mechanical fasteners work, or even adhesive technologies? If none of these apply, consider whether the fume can be reduced through the use of a thinner gauge material or by substituting the welding rods for ones that release less fume.
Which local exhaust ventilation system is best for each individual welding project?
If the hazardous task cannot be eliminated or substituted, following the hierarchy of controls leads on to engineering controls such as LEV. The design and installation of suitable LEV systems is a job for professionals, and SOCOTEC’s occupational hygienists have seen many examples of systems that are not fit for purpose.
Extracted booths will generally offer the most control during welding, with air benches and back draught benches not far behind. The advantage of these systems is that, as long as the extraction is on and the operator has checked they are working, they extract close to the source of the fume without too much reliance on the operator. However, they are generally not suitable for the largest workpieces.
For larger workpieces where continuous wire welding such as MIG is used, on-torch (or on-tool) extraction is preferred. This offers more flexibility, does not rely on the user positioning the LEV correctly and extracts very close to the source. With a greater focus on these systems in recent years, they are becoming more effective, lighter and more comfortable to use. They do, however, rely on being set up correctly in the first place, and can struggle with fillet welding or groove welding in the overhead position.
If the above systems are not reasonably practicable, the best alternative will often be moveable captor hoods, which are ubiquitous in welding areas and are often the first LEV that people think of for welding. Their main disadvantage is that they rely on the welder moving them into the correct position, which is not always possible during a long welding run. They are often seen placed at one end of a large workpiece while the welder is at the other end too far away to gain any benefit, or even placed behind a welder’s head, drawing welding fume straight into their breathing zone. Despite this, they can be effective if used correctly, and there are portable versions suitable for carrying out shop floor repairs.
When is RPE required?
There are three main situations where RPE is required:
- When the LEV does not adequately control exposure, it should be supplemented by RPE
- When welding outdoors, if LEV is not practicable
- When undertaking welding in a temporary work location where LEV is not reasonably practicable, such as some work at height, in which case everybody working in the area should wear RPE
There are numerous types of RPE that welders can use provided that appropriate filters with an assigned protection factor (APF) of at least 20 are used. Powered respirators with an integrated welding visor and clear window are generally considered the most suitable for welding, particularly for periods of an hour or more. These do not rely on a seal and the tinted visor can be raised without lifting the clear window, allowing workers to inspect the weld without being exposed to lingering fume.
Suitable training should be put in place for all control measures so that users can operate and maintain them properly. Personal exposure monitoring should be undertaken regularly to check the effectiveness of any control measures in place and to help determine whether RPE is needed in addition to the LEV. Regular health surveillance and biological monitoring should also be carried out.
If the HSE considers that these expectations have not been met, they have a range of enforcement options at their disposal, such as improvement notices. However, if there is a solid action plan in place to meet this new set of expectations, enforcement action is much less likely.
How can SOCOTEC help?
SOCOTEC’s team of occupational hygienists are fully trained to help employers and their staff to comply with occupational regulations and help eliminate the risk to health within the workplace, including LEV assessments, workplace exposure monitoring (including exposure to welding fumes) and control measure evaluations.
Click here to find out more or contact our Occupational Hygiene team via this form.
Recommended reading
HSE Guidance on welding health and safety: http://www.hse.gov.uk/welding
HSE COSHH guidance for welding, cutting and allied jobs (the “WL” series): http://www.hse.gov.uk/welding/guidance/index.htm
HSE Bulletin: Change in Enforcement Expectations for Mild Steel Welding Fume: http://www.hse.gov.uk/safetybulletins/mild-steel-welding-fume.htm
Breathe Freely welding fume control selector tool: http://www.breathefreely.org.uk/
HSG258: A guide to local exhaust ventilation (LEV) http://www.hse.gov.uk/pubns/priced/hsg258.pdf
HSG53: Respiratory protective equipment at work: http://www.hse.gov.uk/pubns/priced/hsg53.pdf
SOCOTEC is well equipped to help employers and their staff comply with occupational regulations.
Examples of services we can provide include LEV assessments, workplace exposure monitoring (including exposure to welding fumes) and control measure evaluations.
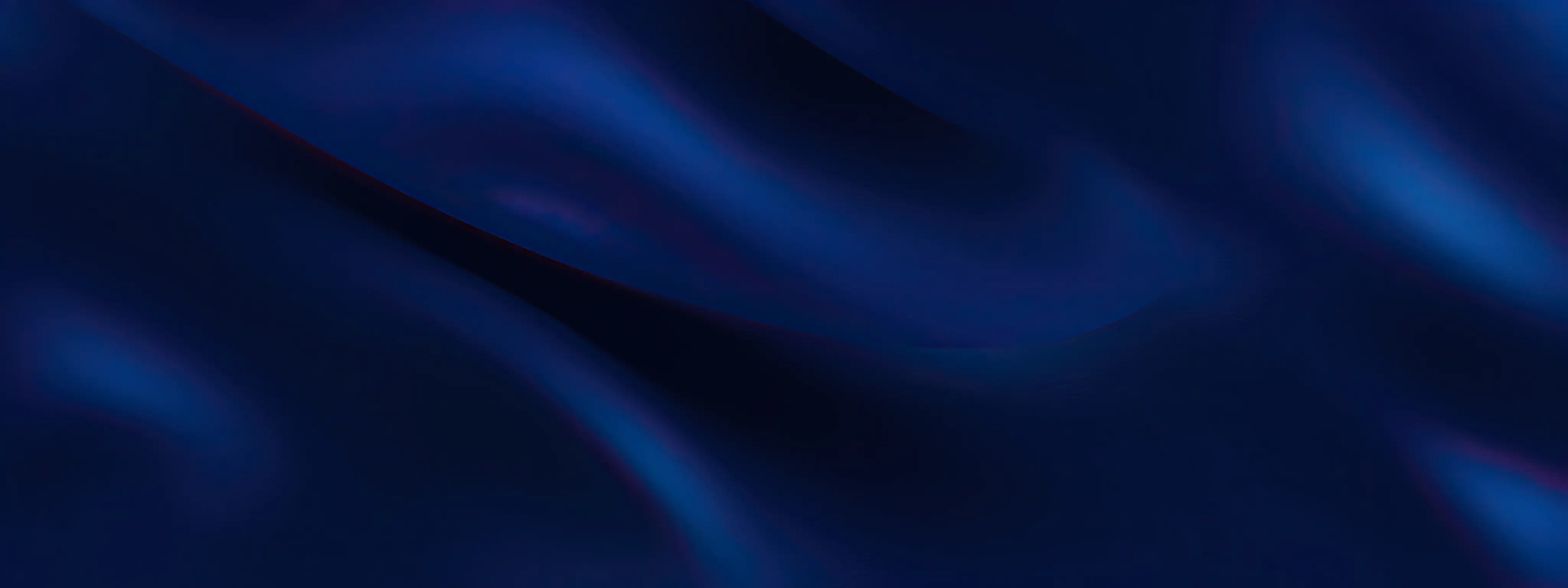
You might also like
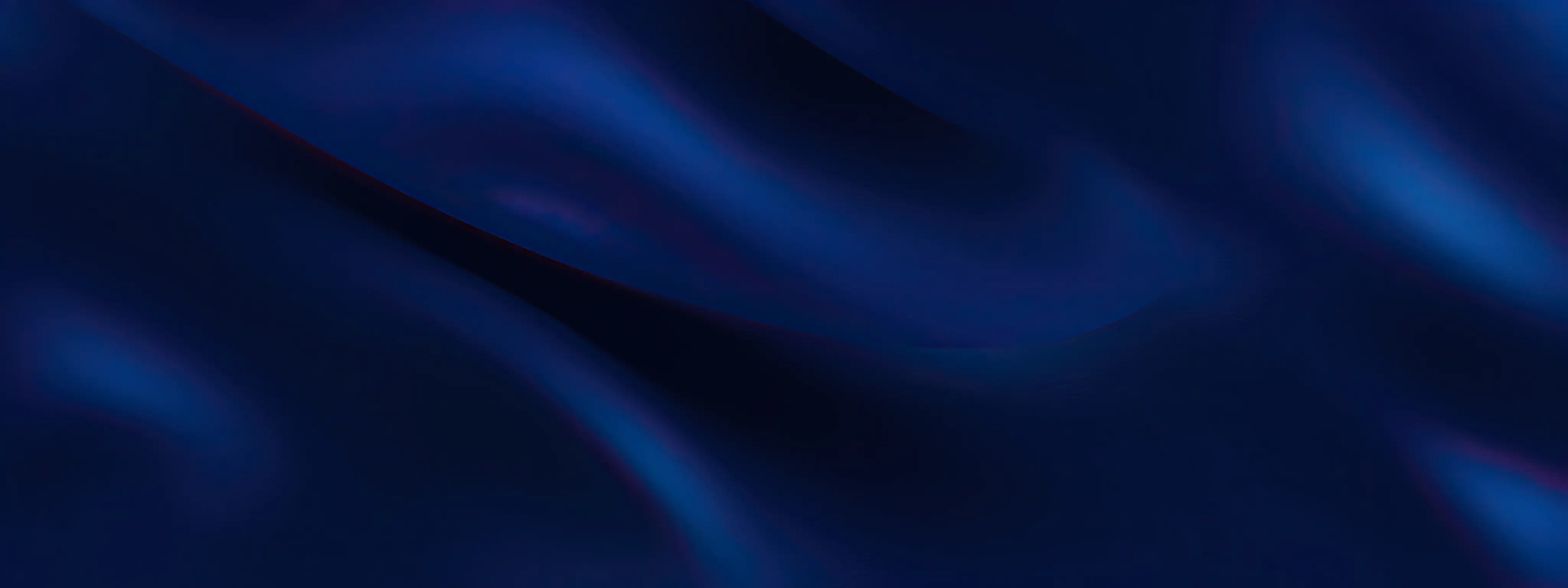
Add new comment