Respirable dust and silica testing play a crucial role in promoting workplace health and safety in the rail sector, particularly when it comes to ballast and sanding activities. These processes not only help identify potential health hazards but also work towards minimising the risk of illnesses and injuries that may arise from the work environment.
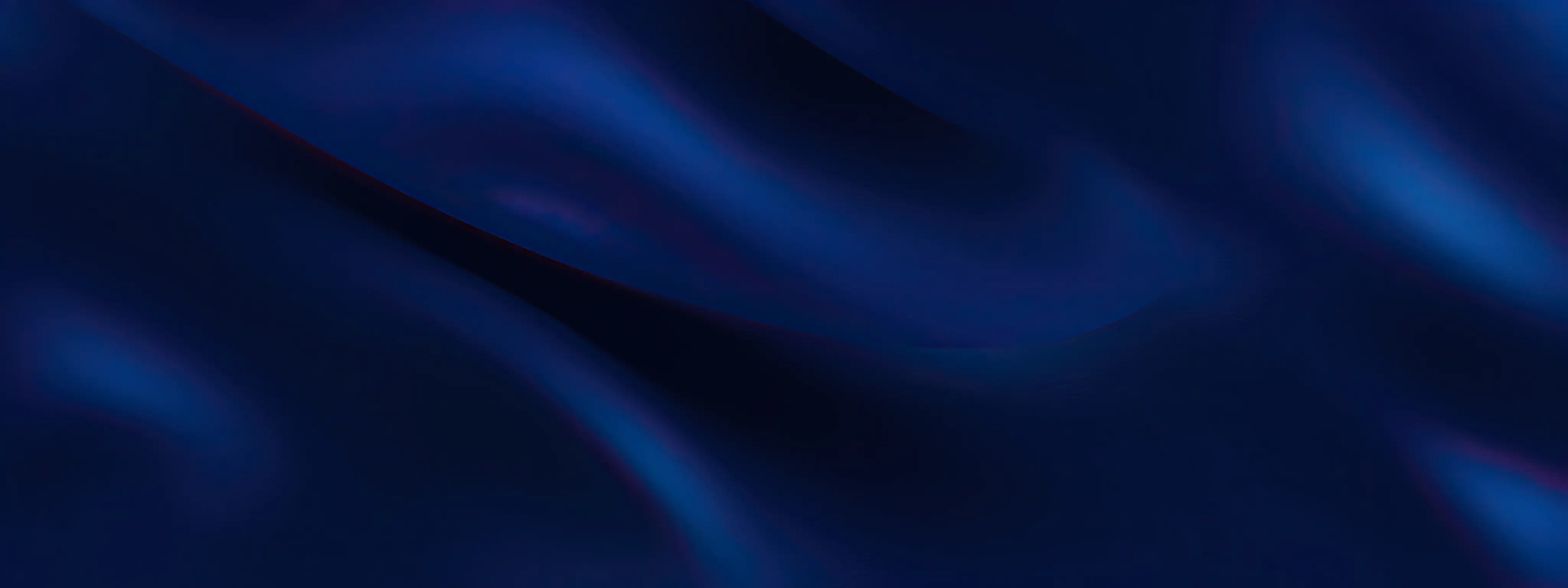
Various industrial operations generate dust, whether from machining parts or working with raw materials, and the rail industry is no exception. It's essential to recognise that both workers and the general public face potential health effects from the inhalation and exposure to this dust. In this blog, we aim to explore these risks and delve into effective control measures that your rail organisations can implement to protect your workforce.
What are respirable dusts?
Respirable dusts are small particles that can be inhaled and cause damage to the respiratory system. In the rail sector, one of the most common sources of respirable dust is ballast dust, which is created when trains pass over track ballast. This dust can contain a variety of harmful particles, including crystalline silica, which can cause respiratory diseases such as silicosis.
What is silica?
Silica, a common mineral found in rocks, sand and clay, becomes a concern when materials containing it are disturbed during activities like ballast or sanding. Fine dust laden with silica is released into the air and inhalation of this dust can lead to lung damage and potentially fatal respiratory diseases such as silicosis. Furthermore, exposure to crystalline silica dust has been linked to an increased risk of lung cancer, tuberculosis, and other respiratory illnesses.
Identifying risky dusts
Inhalable dust refers to any dust with particles smaller than 100 microns which can enter the nose and mouth during breathing and settle in the respiratory tract. Larger particles get trapped in the nose, throat, or branching airways, where the body's natural defence mechanisms eliminate them. On the other hand, respirable dust comprises particles below 10 microns capable of reaching the deepest regions of the lungs, becoming nearly invisible to the naked eye. Different dusts pose varying health risks and can lead to conditions like chronic bronchitis and occupational asthma.
Of significant concern is respirable crystalline silica (RCS), about 1/60th the size of a grain of table salt. Despite being generated in dusty environments, respirable crystalline silica dust remains indiscernibly fine. It enters the respiratory system through the nose and mouth, persisting in the lungs for years. It can cause irreversible lung damage even before symptoms manifest, and the risk of illnesses can continue to worsen even after exposure ceases.
Where do we get silica from?
Silica is present in nearly all rocks and stones, with its concentration varying based on the type of stone. For instance, limestone contains around 2% silica, while granite can have up to 30%, and sandstone can exceed 70%. The amount of RCS generated depends on the stone type and its use.
Certain activities pose a high risk of generating dust containing RCS. For example, cutting concrete without dust suppression can result in elevated levels of respirable dusts, potentially containing up to 70% RCS. Similarly, handling sands in ways that generate fine dust, such as dropping them from a height or blowing them with compressed air, can also produce high levels of dust containing over 70% RCS. Even the use of ballast in the railway industry can be a potential source of dust, particularly during relaying works involving the dropping or movement of ballast, which can lead to high dust levels.
The hidden dangers of RCS dust
When dust finds its way into our lungs, our body's defence mechanisms kick in to protect us. However, when it comes to silica particles, our body's defences fall short. Silica particles are resilient and cannot be broken down by the immune system. Instead, they cause harm by forming scar tissue in the walls of our lungs.
Silicosis, a major health risk associated with RCS dust, results in the development of small, hard nodules of scar tissue in the lungs. This condition takes time to develop, but in cases of high exposure, an acute form of silicosis can lead to death within months. Coughing and difficulty breathing are common symptoms, but the risks go beyond that. Silicosis increases the likelihood of tuberculosis and lung cancer and can even lead to kidney disease, arthritis, and related ailments. Additionally, exposure to respirable crystalline silica can contribute to chronic obstructive pulmonary disease. According to the HSE, occupational lung disease leads to an estimated 12,000 deaths each year and 400,000 working days lost in Great Britain. All of these deaths are preventable through proper controls.
Understanding legislation and exposure limits
The Institute of Occupational Medicine (IOM) recommends strict exposure limits, suggesting that inhalable dust concentrations should be controlled to 5 mg/m3 (eight-hour time-weighted average) and respirable dust to 1 mg/m3 (eight-hour time-weighted average).
Some dusts, including RCS, have specific Workplace Exposure Limits (WELs) assigned to them and exposure must comply with these limits. The WEL for RCS is set at 0.1 mg/m3 averaged over an eight-hour shift, which is approximately equivalent to 1/40,000th of a teaspoon of dust per day.
Moreover, RCS is classified as a carcinogen, where generated as part of a work process, and therefore, despite the presence of a WEL, exposure must be controlled to a level that is as low as reasonably practicable at all times.
The importance of respirable dust and silica testing in the rail sector
One crucial aspect that cannot be overlooked to safeguard your rail workers is respirable dust and silica testing. By conducting these tests, you can proactively identify potential risks and take effective measures to minimise exposure, ensuring the well-being of your employees. This includes implementing a range of safety procedures and providing workers with the necessary personal protective equipment (PPE), such as reliable respirators.
In the rail sector, employers play a pivotal role in identifying potential health risks through these tests and taking appropriate measures to minimise exposure. This comprehensive approach involves implementing engineering controls, safety procedures, and providing workers with the suitable PPE they need. By prioritising these measures, we can significantly reduce long-term risks associated with work-related illnesses and injuries, safeguarding the health and safety of both workers and the wider public.
Sources of RCS dusts in the railway sector
Within the railway industry, several potential sources of RCS dust require careful consideration. One evident source is ballast works, particularly when new ballast is being dropped on-site for track maintenance. The fine dust particles within the ballast can become airborne when it is released from rail wagons or during the movement of the ballast using mobile machinery.
While works involving used ballast tend to generate less dust, it's important to note that packing and tamping activities can still produce dust containing silica, which must be effectively controlled. Additionally, many powered traction units in use on the railway are equipped with sandboxes. These sandboxes allow a small amount of sand to be delivered to the traction wheels, improving grip in challenging conditions such as wet rails or railheads contaminated with leaf mould. However, during the process of filling and testing the sanding equipment in depots, there exists a potential for exposure to sand dust that may contain high levels of RCS dust, which is incredibly fine and often invisible to the naked eye.
Another potential source of RCS dust is during repairs to station platforms or troughing, where concrete materials are drilled or cut using disc cutters or other power tools. The use of power tools can generate significant levels of dust, posing a risk not only to the power tool operator but also to anyone in the immediate vicinity. Furthermore, high levels of fine RCS dust can be dispersed over a wide area, potentially becoming airborne due to wind or during the cleanup process after completing the job.
It's also crucial to consider dust exposure when handling dry ingredients for concrete. There is a potential for exposure during the tipping of sacks and the initial mixing before water is added.
How to minimise exposure to dusts
Minimising exposure to dusts is paramount for creating a safer work environment. To achieve this, the COSHH regulations provide a hierarchy of controls that serve as valuable guidelines. Let's explore these controls:
- Substitute the material with a less hazardous material
- Use engineering controls such as enclosures to prevent the release of dusts
- Provide extraction at the source to capture hazardous dusts before they become airborne
- Use in a manner that minimises dust release
- Use of PPE/RPE.
Wetting materials is a highly effective strategy since wet materials do not generate dust. Pre-wetting materials or utilising fine water sprays can dampen the dust, minimising its potential to become airborne. While weather conditions naturally wet ballast during works, we need to remain vigilant during dry summer months when materials are at a higher risk of producing dust.
When performing platform repairs with disc cutters, water dust suppression can virtually eliminate the dust generated. It is important to remove all dust using wet methods or vacuuming during cleanup, as using brushes or compressed air can worsen the situation by stirring up more dust and increasing exposure risks.
Drilling concrete requires the use of tools fitted with on-tool extraction systems, also known as local exhaust ventilation (LEV). This ensures that dust is captured and removed before it has a chance to become airborne. Whenever possible, operators should position themselves upwind of dust-generating activities, minimising their exposure. Pouring sands or mixing cement should be done slowly into water to reduce dust generation. Adding sand to water and starting the mixing process slowly can significantly decrease the amount of dust produced.
If all else fails, or when other controls are insufficient, the adoption of RPE becomes a last resort. Operators relying on RPE should undergo face fit tests to ensure proper fit and protection. It is important to keep RPE clean and inspect it for any damage before use. For operators who are not clean-shaven, positive-pressure RPE that doesn't require a tight seal around the nose and mouth should be provided to ensure sufficient protection.
Lastly, monitoring should be carried out to identify and quantify potential exposures, enabling valid risk assessments for all tasks. By selecting appropriate controls based on these assessments, we can eliminate exposure and protect the health of all workers. Additionally, comprehensive training is essential to ensure that all workers are well-informed about the risks and equipped with the knowledge to control these risks effectively.
How can we assist your rail business in creating a safe working environment?
We are dedicated to providing comprehensive support for your testing needs in the rail sector. Our range of services includes air sampling and analysis, specifically tailored to ballast and sanding activities. With the help of our experts, we can develop monitoring strategies that suit your specific requirements, ensuring accurate and reliable results.
Our team of professionals can assist you in conducting respirable dust and silica testing, guiding you through the process and helping you interpret the results. We can also provide recommendations on control measures and best practices to minimize exposure to hazardous dusts, ultimately fostering a safer working environment for your employees.
By partnering with us, you can take a proactive approach to workplace safety and demonstrate your commitment to protecting the health and well-being of your workforce. Together, we can ensure that your rail business meets the highest standards of safety and compliance, creating a culture of safety that prioritises the well-being of all employees.
Does your rail organisation require support with occupational hygiene services?
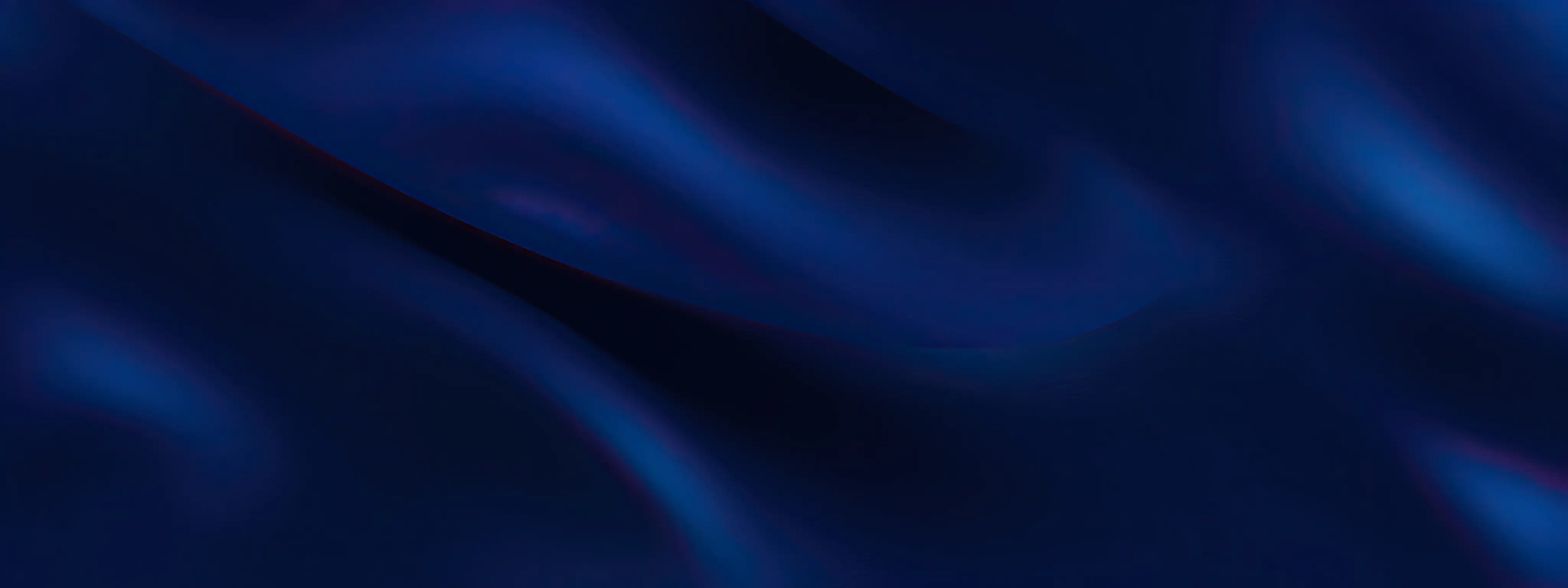
You might also like
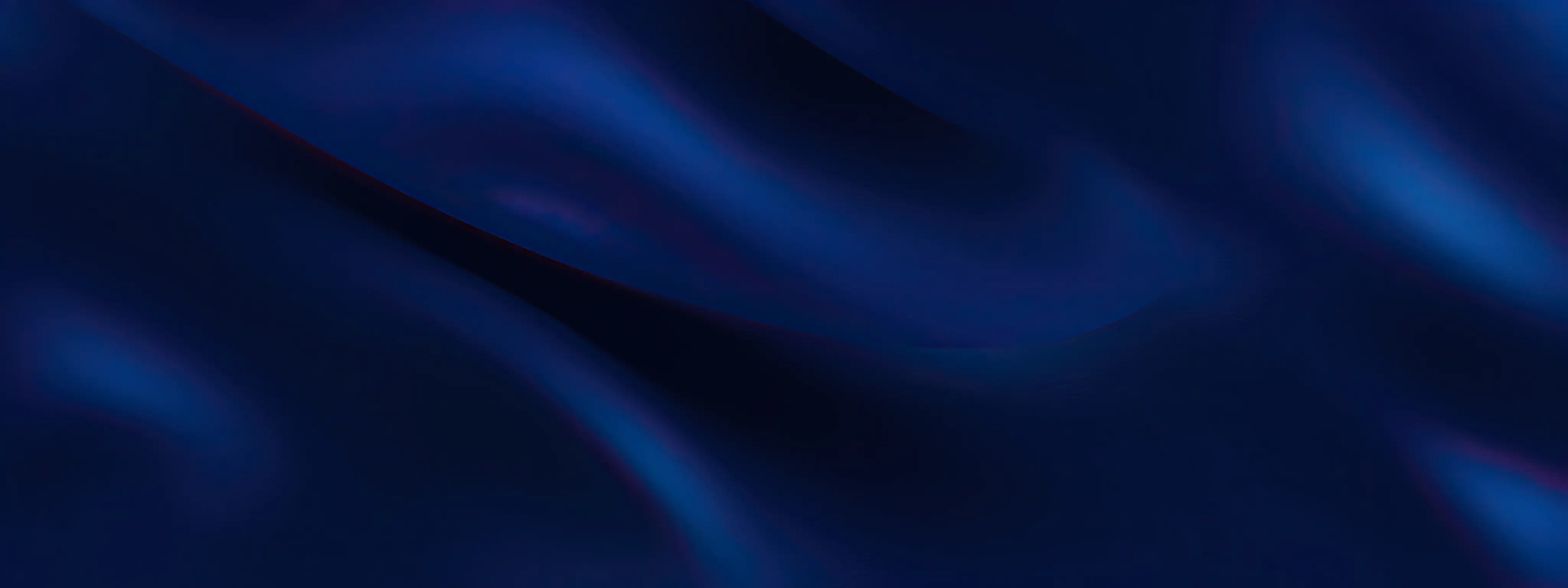
Add new comment