SOCOTEC, the UK’s leading provider of testing, inspection and compliance services, has supported Tata Steel’s Port Talbot steelmaking site with land remediation and enabling works.
Summary of Works
Client: Andrew Scott Ltd via Tata Steel
Project name: Tata Steel's Port Talbot
Places: South Wales
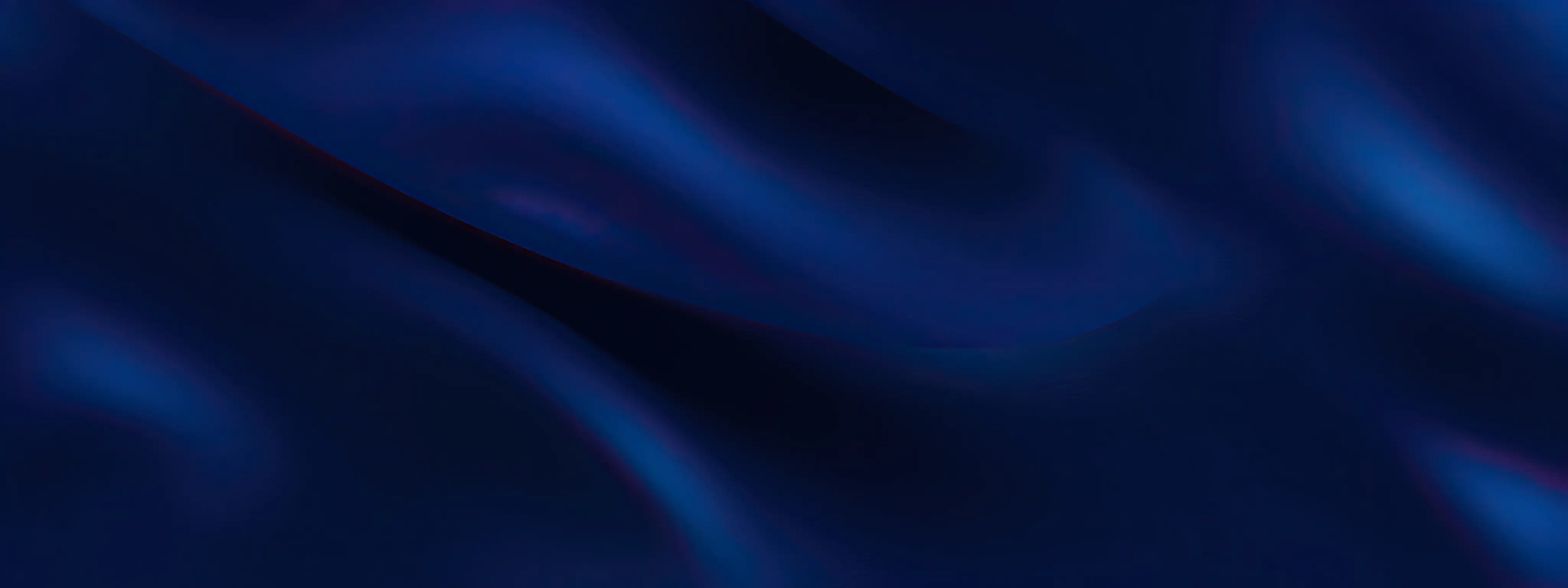
Case Study
Project Details
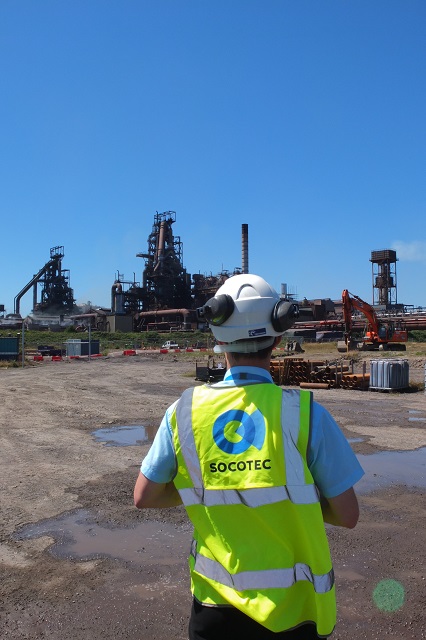
Based in South Wales, the Port Talbot steelmaking site has a long industrial history dating back to the 1920s, and is still producing approximately 5 million tonnes of steel each year. To further invest in the future of the site, a new power plant development was proposed to strengthen Tata’s UK operations in the region which includes the construction of a new turbine house, boiler house and water treatment plant building.
Understanding the distribution of contamination within the land and developing an effective and targeted remediation plan was essential to ensuring that Tata’s Port Talbot’s power plant development plans could be delivered in a compliant and cost effective way.
With experience in delivering a multi-disciplinary approach to earthworks and remediation projects, SOCOTEC’s expertise was called upon by Andrew Scott Ltd – on behalf of Tata Steel – to provide environmental and geotechnical data as well as delivering integrated sampling, on and offsite testing and consultancy services across the project.
Based in South Wales, the Port Talbot steelmaking site has a long industrial history dating back to the 1920s, and is still producing approximately 5 million tonnes of steel each year. To further invest in the future of the site, a new power plant development was proposed to strengthen Tata’s UK operations in the region which includes the construction of a new turbine house, boiler house and water treatment plant building.
Understanding the distribution of contamination within the land and developing an effective and targeted remediation plan was essential to ensuring that Tata’s Port Talbot’s power plant development plans could be delivered in a compliant and cost effective way.
With experience in delivering a multi-disciplinary approach to earthworks and remediation projects, SOCOTEC’s expertise was called upon by Andrew Scott Ltd – on behalf of Tata Steel – to provide environmental and geotechnical data as well as delivering integrated sampling, on and offsite testing and consultancy services across the project.
Site background
Due to the nature of the site, it was anticipated that the ground conditions would cause a number of complex challenges for development. These were in addition to concerns over buried structures and existing plant infrastructure, a legacy of the site’s former coking works heritage.
Prior to SOCOTEC’s involvement, and before enabling works for the development began, a ground investigation took place with 60 exploratory boreholes and trial pits used to delineate areas of contaminant impact. As a result, identified contamination risks included the presence of hydrocarbons, coal tar and metals as well as asbestos in soils – all of which are common for brownfield sites with a heavy industrial history.
Due to the chemicals contained within the land, detailed risk assessment of the site was completed to determine which control and monitoring measures were needed to mitigate environmental and health risks.
Developing a remediation strategy
To address the contamination issues on the site, SOCOTEC developed a remediation strategy which aimed to deliver on two key points: to segregate unsuitable soils while maximising opportunities for soil reuse where possible, and to minimise recontamination of remediated areas.
SOCOTEC produced a Remediation Method Statement and Verification Plan for the site works as well as an accompanying Materials Management Plan to ensure works progressed in line with current regulations and Tata could be assured the works followed best practice.
To maximise soil reuse, SOCOTEC conducted appropriate risk assessments and deployed an on-site mobile laboratory for the chemical analysis of soil samples. In line with the remedial targets methodology, which can be used to set targets for cleaning up contaminated land, separate thresholds were applied to shallow and bulk fill materials so the remediation focus could be on areas that posed the greater risks.
Earthwork challenges and solutions
Beneath the site, a number of buried structures, culverts and pipes made for a tricky excavation of soils. Existing structures and sewers also restricted the handling space, with limited access to different areas of the site.
With plans for the power plant proposed, the excavation and remediation works focussed specifically around the footprints of the new buildings. This area was set within a much larger site, meaning defined excavation areas often crossed over contamination hotspot boundaries. The developed strategy, therefore, had to address concerns and minimise recontamination of the building footprint areas by ‘chasing out’ the site contamination to a point where contamination was no longer significant. To minimise recontamination of excavated and remediated areas, SOCOTEC incorporated control measures into the design which included membranes, perimeter drainage and targeted removal of contaminated waters from the wider area.
The earthworks process created multiple interim 250m3 stockpiles of materials that needed characterisation. SOCOTEC set up a mobile laboratory on site to allow its dedicated analyst to rapidly test and classify the soil and allow the interim stockpiles to be moved to an appropriate holding area (suitable for reuse or quarantine).
SOCOTEC’s mobile laboratory also enabled rapid verification of excavation sides and bases, in addition to verification of ‘chasing out’ contamination that went beyond the planned footprints. The excavation works – and backfilling - was completed in seven strips with each being backfilled with suitable site won soils and then verified as meeting the remediation targets. In tracking the material and verifying which areas of contamination were hotspots for removal, SOCOTEC was able to provide key information to support rapid decision making. Where unsuitable soils were identified, SOCOTEC proposed that the soil was treated to enable to soil to be reused in the pending landscaping scheme.
Common but unspoken problem
The discovery of asbestos in the soil also presented a challenge. Although dangerous when inhaled, asbestos in soils will only present a significant risk if there is potential for asbestos fibres to be released from the soil and subsequently inhaled by site users. When this is the case, remedial measures are needed.
For the site, the presence of asbestos-containing materials (ACMs) in their original form required a licensed asbestos removal contractor to remove asbestos. SOCOTEC’s asbestos team conducted air monitoring to check that airborne fibre levels are below acceptable levels. This took place during earth moving operations as evidence that control measures were being adhered to.
Segregating soils with on-site laboratory
In addition to providing rapid results, the presence of SOCOTEC’s dedicated on-site laboratory service allowed a much greater density of data to be obtained, which reduced the volume of hazardous waste through segregation and maximised material reuse through delineation of contamination hotspots.
However, the samples being analysed were complex matrixes so screening methods alone were not sufficient. Because SOCOTEC was required to test for a wide range of contaminants, the dedicated on site analyst implemented a number of techniques within the mobile laboratory to deliver the required results. Analytical methods included XRF, UV fluorescence, gas chromatography and colorimetry. This allowed low concentrations of key marker chemicals with very low reuse targets to be discriminated from the wider complex hydrocarbon matrix.
To be reliable and provide a sufficient degree of certainty, the application of on-site analysis required a controlled environment and appropriate quality control, coupled with a demonstration of method applicability. The results from the mobile laboratory were validated by SOCOTEC’s off-site laboratory, as per Environment Agency (EA) guidelines. Duplicated samples meant results could be directly compared and correlated, showing sufficient statistical certainty. In doing so, SOCOTEC could reduce the risk of false negatives on site and ensure all results were quality controlled.
Utilising the mobile laboratory allowed SOCOTEC to finely segregate unsuitable soils from the bulk volume of directly reusable soil. Having characterised 7500 m3 of soils as unsuitable for direct re-use, the project progressed to stabilisation trials to treat the soil. The intention is to use the treated soils for landscaping beneath a clean cover system which the risk assessment determines would not pose any risk to future users of the site. The earthworks was carried out in accordance with CL:AIRE Definition of Waste Code of Practice (DoWCoP), along with the Materials Management Plan in place.
Effective management of potentially contaminated soils, materials handling and material re-use can support a project in timeliness and cost-effectiveness. SOCOTEC was able to implement an approach to maximise soil reuse, which – in effect – saved Tata Steel significant sums of money in hazardous waste disposal fees.
Partnership and development
SOCOTEC also conducted environmental and workplace monitoring throughout. This included airborne fibres for reassurance over the asbestos risk, as well as boundary PM10 and depositional dust monitors. Monitoring close to offsite noise receptors ensured that impact on the environment was kept to a minimum and in line with regulations.
Paul Tilley, operations director, Environment and Safety, said:
“The development at Tata Steel’s Port Talbot site is still ongoing. Across the UK, contamination of industrial sites is a common occurrence due to its very nature and it’s fundamental that developers and contractors have the right information about the nature and location of any contamination on their site. With the right procedures, methodology and guidance, however, contaminated land can be cost effectively remediated as part of the general enabling works phase to ensure both project delivery and minimal risk to both the environment and human health. The remediation of this land not only demonstrates Tata’s dedication to ensuring environmental compliance, quality and safe practice, the end results will bring benefits to the region for years to come.”